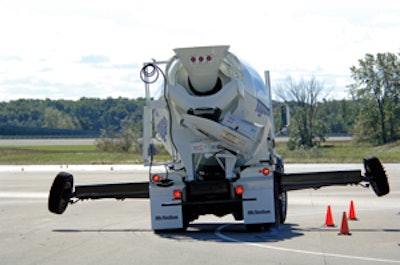
If you operate any type of truck with a high center of gravity, you need to address the potential of a rollover accident. While operator training helps mitigate the chances of a rollover, even the best drivers are subject to unavoidable emergency maneuvers and momentary lapses in attention that can lead to major incidents. But new technology in the form of electronic stability systems is emerging that will minimize these risks.
Electronic stability systems integrated into the anti-lock brake systems (ABS) of on-highway tractor-trailer rigs have created quite a buzz. These systems will not prevent all accidents, but they do promise to significantly mitigate jackknifes and rollovers.
Until recently, only on-highway tractors and trailers could benefit from such systems. Unlike over-the-road tractors, vocational trucks feature wheelbases all over the map, as well as different axle configurations and spacings. This creates a unique challenge since the software that controls the stability management system must be customized for each variation.
"Engineering this technology for tractors is more straightforward," says Tom Kelly, vice president of marketing, Mack Trucks Inc. "But as a leader in the heavy-duty vocational market, we're committed to getting this technology in the hands of mixer and dump customers as soon as possible. We targeted mixers initially per customer demand."
Ready-mix fleets quickly see the value these systems promise. "Concrete customer demand for stability protection is strong because mixers, in general, are recognized to have a high center of gravity and carry dynamic loads," says Steve Ginter, vocational products marketing manager.
Other applications will follow. "We're working very hard with our partner Bendix on other vocational applications, as well, to make the technology widely available," says Kelly.
How it works
The stability system developed by Mack's partner, Bendix Commercial Vehicle Systems LLC, has been named Mack Road Stability Advantage by Bendix (Mack RSA). It uses the existing ABS wheel speed sensors, along with steering, yaw and lateral acceleration sensors. Information from these sensors is transmitted to an Electronic Control Unit (ECU), which constantly compares performance models to the vehicle's actual movement. If critical threshold values are approached, the system will intervene by deactivating the throttle and selectively applying the appropriate brake or brakes.
When negotiating curves, sudden lane changes or obstacle avoidance maneuvers, this system reduces the potential of a rollover and reacts faster than a person in most situations.
However, the electronic stability system cannot change the laws of physics. The system must reduce speed to prevent a rollover. If you enter a 30-mph corner at 50 mph, the system may apply the brakes at full pressure and it still may not be enough to slow the vehicle down in time to prevent the rollover.
Ride impressions
Mack Trucks recently invited Equipment Today to a demonstration at the Las Vegas Motor Speedway. A tractor/trailer rig and a ready-mix truck were both equipped with Mack RSA, which could be turned on/off, and specially-designed outriggers to keep the vehicles from rolling over.
A course was laid out where we were allowed to ride around a tight-radius corner that simulated an on/off ramp. Another course simulated a high-speed lane change. First, we went through each course with the system turned off, then with the system turned on to compare the results.
Using the ready-mix truck with the system turned off, the driver approached the on/off ramp with a little too much speed. The truck proceeded about halfway through the corner before the inside wheels came off the ground and you could feel the truck being held up by the outside outrigger.
On the next pass, the Mack RSA was turned on and the ready-mix truck approached the on-ramp curve at the same speed.
This time when the turn was initiated, you could feel the brakes being automatically applied while the truck remained at a safe and stable speed. The driver continued to hold the accelerator pedal down, but the Mack RSA intervened by cutting the throttle and applying the brakes to keep the truck within the safe pre-programmed parameters.
Next, we initiated an aggressive high-speed lane change with the system off. The ready-mix truck bucked pretty hard as it rapidly rolled onto the outrigger and bounced back upright on the wheels.
Finally, the system was turned on and the aggressive lane change was initiated at the same speed. This time, the RSA cut the throttle — despite the driver keeping the accelerator pedal depressed — and it applied select brakes to keep the truck under control. You could feel the truck aggressively brake from the cab. The truck remained upright and stable.
In both scenarios, the Mack RSA returns throttle control back to the operator as soon as it deems the operating parameters are again within the safe zone. The operator can always override the brakes with additional brake pressure. To ensure safety when the system engages, the rear brake lights do illuminate to warn other drivers that you are slowing down.
The demonstration really accentuates the benefits all fleets will receive as this technology becomes widely available.
A useful reporting tool
In addition to preventing rollovers, the Mack RSA can help identify incidents that could have resulted in a rollover. Every time the stability system intervenes to prevent a rollover, the event is logged into the ECU's history. It is tagged with the vehicle speed and engine hours.
A counter indicates the level of intervention that occurred. By downloading this information via Bendix ACom 5.2 diagnostic software, you have a record that can be used as a tool to provide necessary training and increase fleet safety.
Application challenges
Why isn't this system going to be immediately available on all vocational Mack trucks? Several variables affect the RSA program in the ECU, which determines when an intervention is necessary. These include the weight, center of gravity location, wheelbase, suspension stiffness, etc. This means that the program in the ECU must be customized to specific configurations, a daunting task when you consider all of the wheelbase, suspension and body packages available in our industry.
First to witness the benefits will be the ready-mix fleets, followed by the dump truck fleets. "We're proud to be the first heavy truck manufacturer to offer this technology to vocational customers," says Ginter.