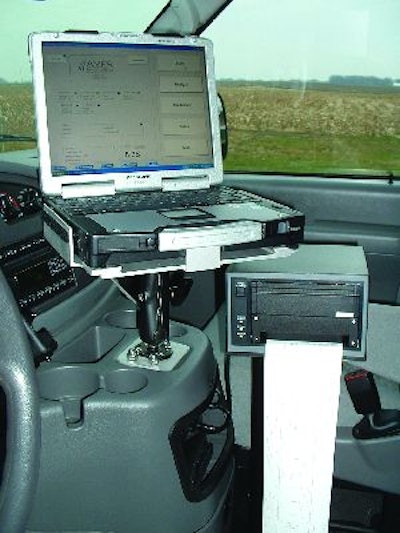
What are the critical components to the paving train? Historically, the concrete contractor would typically mention the slipform or bridge paver, placer/spreader and the texture/curing machine. Off the top of his head, the asphalt contractor would probably point out the paver, rollers and rolling pattern, and probably the material transfer vehicle.
With today's more stringent ride standards and contract incentives being tied to smoothness, a relatively low-cost, high-tech tool is becoming an increasingly valuable part of the paving train. Both concrete and asphalt contractors are using Lightweight and High-Speed Profilers as in-process tools to help crews deliver a higher quality, smoother pavement surface, which helps the contractor to realize incentive payments.
"Smoothness has always been important for us and the industry as a whole," says Larry Shively, vice president of the Shelly Company, Thornville, OH. "The advent of profilers allows us to get profile numbers to our foremen quicker and with more accurate results, so we can deliver a better product to our customers."
A subsidiary of Oldcastle Materials, Shelly Company has more than 20 asphalt paving crews operating from four regional offices ? Twinsburg, Findlay, Columbus and the Thornville main office ? in Ohio. Currently, the paving contractor owns three Ames 8200 High Speed Profilers for the four regional offices. The profilers roam jobsites within a region to measure the profile of the pavements being paved by the crews.
The key to success
These machines are not just measuring the final numbers of the surface lift to ensure it meets the ride spec. No, Shelly Company's profilers are being used as in-process tools, measuring the pavement's profile after nearly every lift ? whether leveling, base or binder ? to ensure the smoothness numbers of the surface lift will be where they need to be.
"The profiler is a very important tool for our paving operations," mentions Shively, who is also responsible for quality control for Shelly Company.
The contractor has incorporated the use of profilographs and profilers into its paving operations for nearly a decade. Shelly Company started with the California type profilograph, but it quickly upgraded to the Ames Engineering Model 6200 Lightweight Profiler to speed up the pavement profiling process. More recently, the company has been using High speed profilers, which allow profile to be measured at highway speeds.
"Our profile crew drops in, does a quick analysis and gives the foreman the information to make any paving adjustments necessary," Shively explains.
These corrections can range anywhere from changes in the way a crew is unloading trucks to adjustments in the rolling patterns. The analysis has also helped Shelly Company to uncover pre-existing conditions in the road, which allows the contractor to go back to the project's owner early on to discuss possible changes in the pavement's design. In more extreme cases, the company may even bring in a mill on the base or intermediate lift to remove high spots.
The key is that Shelly Company uses the profiler as an in-process tool. The profilers not only help give the contractor smoothness numbers for the entire pavement, the software operating the profiler allows crews to pinpoint the locations of trouble spots.
"The technology allows the storing of information as fine as every inch of the surface," says Jon Klatt, sales manager for Ames Engineering. "Contractors can view International Roughness Index (IRI) numbers for specific areas in 50-foot increments."
Shively agrees with Klatt on the value of the spec area analysis of the profilers. "They are very helpful tools for conducting the forensics on the road. We can isolate problem areas and give our crews the necessary information to correct the issues," he adds.
While Shelly Company is now sold on the value of using profilers as an in-process tool, it wasn't always. Shively admits the main reason for initially using profilographs years ago was that it was required by the Ohio Department of Transportation (ODOT). But the company quickly saw the tool's advantages, and the use of profilers has now expanded to non-ODOT projects such as commercial, city and county paving.
"The use of profilers makes us more aware of the product we are supplying our customer and more conscientious of what influences smoothness," Shively says. He is quick to point out that Shelly Company has always delivered a quality product, but by incorporating profilers into the company's quality control routine, the product is now even better. It helps them achieve bonus level work, and they also have a database of numbers to submit to associations for award consideration in Ohio and on the national level.
Evolution of technology
Nearly a decade ago, paving contractors had only one choice for obtaining the profile of a surface, the profilograph. While these machines would give contractors the necessary profile numbers, they were time consuming to use.
"The profilograph was the tool of the trade, but since its speed ranged from 1.5 to 3 mph, it was impractical for in-process monitoring of smoothness," Klatt mentions. As a result, most paving contractors would use the profilograph to measure the final surface numbers.
The introduction of John Deere Gator-mounted lightweight profilers, like the Model 6200 Profiler nearly seven years ago, gave paving contractors a more flexible tool that could be used in a variety ways.
"Our Lightweight Profiler allows contractors to measure the pavement's smoothness at speeds ranging from 8 to 15 mph, more than five times faster than profilographs," says Dustin Reid, product manager for Ames Engineering.
This results in shorter lane closure times for profiling and allows contractors to begin to incorporate the profiler as an in-process tool for their paving operations, just like the Shelly Company. "It also helps to enhance safety, since the crew leaves the work zone quicker," mentions Klatt.
The concrete industry and concrete paving contractors were quick to adopt the technology. It gave them an in-process diagnostic tool to help enhance the pavement's smoothness.
"Its relative light weight enables contractors to get on the slab the next day to collect profile data," Reid explains. "This data is critical to help determine and diagnose problems with string line setup, paver controls or concrete placement in front of the paver."
A few years after the introduction of Lightweight Profilers, the industry began to see the first high speed profilers like the Ames 8200 models owned by the Shelly Company.
Supplied in a "kit" form, these profilers do not require a specialty vehicle, as this new generation unit mounts quickly to any two-inch hitch receiver in the contractor's own vehicle fleet.
Higher speeds enable a profile to be efficiently taken on every lift and at multiple sites. Shelly Company uses its three profilers to measure smoothness for 20 paving crews.
"The higher speeds allow us to cover more paving crews in a shorter period of time," Shively says.
Variety of configurations
Over the years, the technology of profilers has advanced to improve their accuracy. "The information captured by today's profilers is much more accurate than that from profilographs," Klatt says.
The data gathered offers a true elevation profile that plots a California profilograph or rolling straightedge; and it calculates the International Roughness Index (IRI), a Profile Index (PI), Half-car Roughness Index (HRI), Ride Quality Index (RQI), and Ride Number (RN).
According to Reid, more states are going to IRI, since it better reflects what the public feels when driving on a road. "It's based on an algorithm that more heavily rates the short wavelengths like bumps at an expansion joint, but it still counts the longer wavelengths like rolling undulations," he says. "It's more of a true ride reflection."
To help obtain a more accurate IRI number prediction, Ames Engineering developed dual sensor profiler models, which make up the majority of the company's sales. These dual sensor models profile both the left and right wheel tracks as compared to only one wheel track measured with a single sensor system. This results in a more accurate smoothness reading.
Profiler manufacturers have also enhanced laser technology to improve profile accuracy. Initially, single point lasers were used to measure the pavement's smoothness, but contractors soon discovered that a pavement's texture can affect profile numbers.
"The texture in concrete surfaces and some SMA and open-graded asphalt mixes can falsely elevate the numbers," Klatt says.
To combat this, profiler manufacturers have developed multipoint laser systems like the RoLine sensor from Ames Engineering to analyze a broader surface footprint. "The single point sensor is good for tight asphalt surfaces, but the RoLine monitors 100 points across the surface, so it eliminates texture deviations," Reid explains.
Profiler software is another area where manufacturers are focusing to aid contractors in diagnosing roughness in pavements. The system's odometer mode enables contractors to precisely locate any areas of localized roughness that require attention.
"For today's paving contractor, the name of the game is accuracy and smoothness," Klatt says. "With the types of profilers and available options on the market, the contractor is able to quickly obtain accurate smoothness numbers by using the profiler as an in-process tool, and the crew uses this information to take the necessary corrective actions to deliver a smoother final product and maximum profits."
Rick Zettler is a freelancer from Cedarapids, IA.