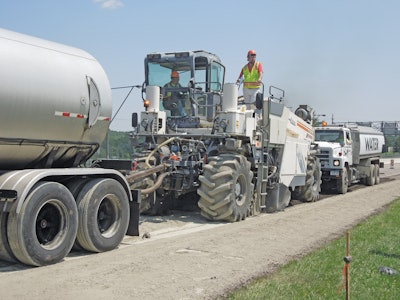
If you’re not familiar with what foamed asphalt is, it might be something you should look into. That’s exactly what the Delaware River Joint Toll Bridge Commission (DRJTBC) and the engineering firm, Cherry, Weber & Associates of Pennsylvania and New Jersey, did when designing the New Hope-Lambertville Toll Bridge project. The decision to use foamed asphalt enabled the DRJTBC to reduce the pavement reconstruction costs by 60 percent and overall project costs by roughly 30 percent.
The area being worked on along Route 202 serves as a pathway across the Delaware River between Pennsylvania and New Jersey. The need for the project was based on inspection reports and a draft concept study that found a series of deficiencies in the approach roadways, approach bridges, and nearby highway exit and entrance ramps in the vicinity of the toll bridge.
Issues addressed by the overall project included spalling concrete, faulty deck joints, rusty and corroded bridge bearings, and fatigue (alligator) cracking, potholing, and block cracking of approach roadways and ramp surfaces.
“Based on the condition of the pavement, the HMA pavement rehabilitation began to evolve into a full reconstruction,” says Greg Bitsko PE, senior director of structural engineering at Cherry, Weber & Associates.
Why foamed asphalt?
Cherry Weber was tasked by the DRJTBC to develop a project that had a 15-year design life for the pavement, that would not cause a significant change in the road elevations and that would minimize traffic disruption.
“We suggested foamed asphalt because other jurisdictions had success with it and achieved significant cost savings on similar types of projects. Based on the information provided by Cherry, Weber, the DRJTBC agreed to consider a foamed asphalt alternate.”
While the foamed asphalt repaving technique was invented several decades ago, its use in this region has been extremely limited. So the project was advanced as either a conventional project or a recycling project. Contractors were given the option to bid one method or the other.
“Because it’s new, there is no one in the immediate area that has the equipment you need for the foamed asphalt,” says Bitsko. “The commission was a little bit concerned about seeing the cost savings some of the other jurisdictions saw due to the mobilization of contractors from farther away.”
This competition gave Cherry Weber a pretty good idea on what type of cost savings they would see if they went with foamed asphalt. With four bids for foamed asphalt and one conventional paving bid, the cost saving possibilities were immediately apparent.
“The foamed asphalt low bid was $1.1 million and the conventional was $2.8 million,” says Bitsko. “You save $1.7 million on the project versus doing it conventionally. That’s a 60 percent reduction in construction costs.”
Paving the way
Since this process is so new, Cherry Weber was left with many questions on how to proceed. “The challenges on this job were two-fold,” says Bitsko. “First, how do you design it? And then, how do you develop construction specifications for it? The DRJTBC follows either NJDOT or PennDOT design and construction requirements and neither NJDOT nor PennDOT at the time had any guidance whatsoever on foamed asphalt recycling.”
The first task was to develop both mix and pavement designs. “We relied extensively on our equipment supplier, Wirtgen’s book on mix designs and the requirements for preparing the mix. Then went back to the 1993 AASTHO pavement design process, so at least that part was pretty straight forward,” says Bitsko.
Next, Cherry Weber had to develop the construction specifications. “What do you do? How do you check it? What are the tolerances? That part was pretty much wide open to us,” says Bitsko.
Luckily, they had a friend in the business who could help. Bitsko says the Alaska DOT uses foamed asphalt almost exclusively on their road and airport projects. “We were coordinating with them once a week to figure out what worked,” Bitsko laughs. “We ended up using their construction specifications for foamed asphalt, modified for this job. That was the real challenge to it, trying to pull bits and pieces and get the research from CalTrans and different jurisdictions that did this and try to weave them into coherent construction specifications for this job.”
Working smart
One of the most important factors to choosing this method was the amount of truck traffic the foamed asphalt paving train would save. “New Hope is a very tourist friendly area,” says Bitsko. “Work was being done during the summer, the peak of their busy season. We knew this method would reduce truck traffic significantly.”
In a traditional paving job, there is milling and excavating to be done on the roadway where you’re working. In this case though, they couldn’t really close the road for any significant length of time to accommodate that.
“In a traditional reconstruction job, you have a excavator digging out the existing asphalt and loading it into a truck to haul off site. You then have an 8 to 10 inch excavation next to your traffic lanes. With this much of an elevation change, barrier curb is then needed.”
“In this job, we milled 2 inches off the surface to help maintain road elevation, but all the rest of the materials were recycled in place. They never left the site,” says Bitsko. “You’re using most of what’s out there and minimizing the amount of material trucked off of or into the site.”
The process of “foaming” the asphalt involves taking the existing material on the roadway, pulverizing it, then adding new liquid asphalt to it. A small amount of water is then injected in to the liquid asphalt, which causes the material to expand. When all is said and done, you have created a soil aggregate that has been stitched together with the asphalt. You’ve creating an asphalt stabilized soil aggregate base.
On this particular job, a Hensley tri-cement spreader truck was used to apply the required cement in advance of the recycling train. An asphalt cement tanker truck was pushed in front of a Wirtgen 2500s Reclaimer/Stabilizer. The PG64-22 hot liquid AC was introduced directly into the Wirtgen during pulverization. The recycler is then pulling a water tanker, which is feeding water into the machine, providing the material for the foaming process.
“Speed was of the essence for us,” says Bitsko. “With this process you’re running a machine over the road, pulverizing the material and not creating any significant elevation changes. That is where we cut down on traffic control and trying to change lane patterns.”
The rest of the work mirrored that of a traditional paving job, Bitsko says. James D. Morrissey, Inc. of Philadelphia was the primary contractor for the work, along with Reclamation LLC of Kingston, N.Y. as a sub-contractor. The equipment used after recycling was an Ingersoll SD-105 vibratory pad foot roller, a Hamm HD 130 steel vibratory roller and a Cat CB 614 steel vibratory roller.
After recycling, the road was given a HMA Superpave asphalt overlay per NJDOT or PennDot requirements.
“The work can be done much quicker than with traditional paving methods since it’s a much more compact operation,” says Bitsko. 33,000 square yard were recycled and re-paved in 25 working days.
Savings worth celebrating
Due to the compact operation of the paving train, the job was able to cut truck traffic by 80% over a traditional job. “We had about 270 truck trips, due to the milling and the new HMA wearing course being brought in” says Bitsko. “If we would have boxed it out, there would have been over 1,400 truck trips. So with this system, you’re not damaging roads to build roads. You’re keeping trucks out of local intersections and away from tourists.”
The project, which marked the first time that foamed asphalt technology was used at a Commission facility, won several awards. It was recently given the 2013 Honor Award from the New Jersey chapter of the American Council of Engineering Companies. They recognized the full-depth pavement recycling work that was the core component of the 2013 project. The award was bestowed March 12 at a ceremony in Jamesburg.
As a result of the award, the project was automatically given consideration for the ACEC national award. The project received a Recognition Award from the national ACEC in late April.
The project won the 2014 Distinguished Engineering Award from the New Jersey Alliance for Action, a construction advocacy organization — this award was received during a ceremony in Holmdel on Jan. 30.
Finally, the project won one of three national recycling awards from the Asphalt Recycling and Reclaiming Association at their annual conference in February of this year.
“The project demonstrated that it is possible to successfully stretch our scarce resources and introduce green construction into heavy highway work,” says Bitsko. “It exemplifies the current trend to get in, get it done and get out. It is hoped that this project will serve to launch the (foamed asphalt) process in this region, which will be a benefit to all.”
Bitsko foresees this process being used in a greater capacity in the future. “We have a lot of interest in this process,” he says. “We think it would be a big boom for municipalities who have roads in poor condition and are just overlaying them right now, but they may need more extensive work. If we can show a cost effective way to reconstruct a roadway, rather than just overlay it, then hopefully they will see that this is the way to go.”