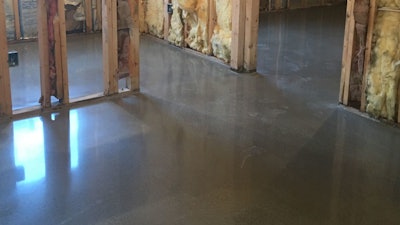
In legend the philosopher’s stone was an alchemical substance that turned base metals into gold. Wars were fought, and tomes were written in the search for that legendary substance. The building owners of today are in search of a remedy akin to the philosopher’s stone of yore, a remedy that can make a worn concrete floor shimmer like gold. Modern concrete polishable overlays just may be the solution.
Concrete is the top man-made building material in the world. Concrete floors have dominated buildings throughout the US and the world at large for well over a century, and those concrete floors have been used and abused for decades. They’ve been covered with VCT and ceramic tile and LVT and linoleum. They’ve been covered with carpet and coated with epoxies. They’ve been soaked and sealed with oils and urethanes and silanes and silicas. These floors have been continuously re-done and re-purposed, but those concrete floors aren’t ageless… they’re aging.
At a point in a concrete floor’s life cycle it begins to morph into a weathered surface that has been stitched and coated, a Franken-floor just like Mary Shelley’s monster. Building owners and managers have traditionally run from that monster and gone to more coatings or coverings to hide the sins of the past. However, today’s marketplace demands a different Industrial Caulk and Seal takes the time during the preparation phase to remove, repair, or patch damaged surfaces prior to application. Following the mechanical preparation of the substrate, that substrate must be primed to ensure adequate adhesion of the final overlay.Industrial Caulk and Seal
What is a Polishable Concrete Overlay
Concrete overlays are not new. In fact, floor re-surfacers of varying types and applications have been around since the early 20th century. In the early 1930’s, a British chemist, John Crossfield, was the first to patent a concrete overlay consisting of both Portland cement as well as latex and naturally occurring rubber compounds. Crossfield’s invention wasn’t intended for floor re-surfacing but for ship deck resurfacing on an aging British fleet. Crossfield’s company, Surfacing Products, and his re-surfacing patents languished in obscurity until a group of investors purchased the entity and Crossfield Products Corporation was born.
Crossfield Products Corporation is generally considered the godfather in the world of cementitious overlays and still exists today. As the company continued to grow throughout the 20th century, they engineered a Portland based overlay that, combined with the latest and greatest epoxy and polymer resin technology, could be used to resurface concrete floors and withstand heavy duty use. By the 1970’s Crossfield Products purchased the company Miraco and transformed Miraco’s Miracote into an all new line of products and overlays for the growing concrete overlay market. Miracote exists today as a worldwide leader in cementitious overlayments.
While Crossfield may have Polished concrete overlays are relatively fast setting with initial set occurring within the first 20-30 minutes and final set falling directly behind at 40 minutes to 1 hour depending on temperature and humidity. Most systems reach compressive strength of 3000 PSI in 1 day and final strength within 30 days.Industrial Caulk and Seal
The Evolution of Polishable Concrete Overlay Products
Concrete overlay products have evolved rapidly throughout the last decade, and among the manufacturers on the cutting edge of this fledgling industry is SpecChem LLC. Though relatively new to the decorative concrete world, SpecChem has deep roots in construction chemicals and has set the industry standard in product innovation. SpecChem’s brand new SpecLevel PCT is no exception. SpecLevel PCT is a flowable cement based self-leveling topping that can be polished as early as 24 hours after initial application. SpecChem’s SpecLevel PCT can be used in a variety of applications, wet or dry… indoor or outdoor, and accepts both integral color and concrete dyes or stains. Keith Fleming and Mike LeMark with SpecChem are excited by the prospects offered with SpecLevel PCT and feel that SpecLevel PCT will rapidly become the benchmark in polishable concrete overlay products.
The Preparation Process
Industrial Caulk and Seal has been a leading contractor in the polishable overlay world since the very beginning. Victor Botley, Chief Operating Officer with Industrial Caulk and Seal, shared insight into the polishable overlay world and the best practices in providing a great end product. “Surface preparation is the key to a finished floor”, states Botley, “if your floor has been inadequately prepped or if the epoxy base coat was marginalized the final floor will never meet expectations.”
Botley’s conclusions are substantiated throughout the polished concrete industry. All reputable polished concrete overlays require surface preparation as a critical component to the floor system. The prepared floor must meet the required concrete surface profile (CSP) noted in the products technical data sheet. Requirements range from a CSP 3-5, and the installer needs to prepare the surface accordingly. The International Concrete Repair Institute (ICRI) manufactures and retails a set of concrete surface profile chips which can be used as a comparison tool on the prepared surface. The correct surface profile is achieved by mechanical means much likeAs a self-leveling flowable compound the overlay mixing and pouring process is relatively straightforward. The overlays are traditionally in bag form and are designed for small batch quantities, though some contractors choose to work larger floors with a specialized pump truck. .Industrial Caulk and Seal
“Another key component to surface preparation,” continues Botley, “is sound, clean concrete.” Industrial Caulk and Seal takes the time during the preparation phase to remove, repair, or patch damaged surfaces prior to application. Following the mechanical preparation of the substrate, that substrate must be primed to ensure adequate adhesion of the final overlay. Primers are available from most manufacturers in both latex and epoxy variations. However, experienced contractors tend to rely on the epoxy version. Once applied to the mechanically prepared substrate, sand must be broadcast into the primer to the point of refusal as the primer sets. “Sanding the primer is critical,” Botley concludes, “turn the floor into a beach.” The sand broadcast step cannot be overlooked or minimized. The overlay systems rely heavily on both the surface profile achieved mechanically and the added surface profile achieved from the sand broadcast.
The team at Industrial Caulk and Seal also stresses an in-depth analysis of the floor surface to verify that a given floor is the right candidate for a polishable concrete overlay. “These worn floors weren’t finished using modern construction methods. There will be bellies and high spots,” states Botley. This is of particular importance in the polished overlay world as some polishable overlays can be placed as thin as 3/8” and are of a self-leveling nature. Should the contractor not have scrutinized the substrate prior to application, there is a very real possibility that the overlay may not meet the minimum depth requirements within a given manufacturer’s system at a high spot. Without that scrutiny, a contractor may grind through the overlay with a planetary head grinder and expose the old floor during the grind or polishing steps that are integral to a great polished concrete floor. Specific attention must be paid to door thresholds and other integral building components, as well. Most polishable overlays have been engineered to mitigate down time on a floor surface and are able to be polished 24 hrs. after placement.Industrial Caulk and Seal
Overlays in Application
After a contractor has completed the substantial surface preparation the overlay itself is the next hurdle ahead. As a self-leveling flowable compound the overlay mixing and pouring process is relatively straightforward. The overlays are traditionally in bag form and are designed for small batch quantities, though some contractors choose to work larger floors with a specialized pump truck. The team at Industrial Caulk and Seal tends to favor Hippo mixers for mixing, pouring, and placement even on larger floors. “If we are faced with a large floor, we may employ multiple mixers and mixing attendants,” Victor Botley states, “The perfect finished floor is our ultimate goal and we only work in batches that we can control effectively. It’s imperative to phase the work are to provide continuous placement wherever possible and eliminate unnecessary transitions or cold joints.”
As the overlay is poured experience contractors use a gauge rake and spiked rollers. The gauge rake ensures minimum thickness, and the spike roller immediately removes entrapped air. As the compounds are designed to be self-leveling troweling is unnecessary, but often a smoother may be employed to coax the material to the final level. Most polishable overlays allow the use of aggregates in the mix to both extend the material and achieve a unique final look. It’s important to note that the final product will be ground and polished, and that some or all these added aggregates will be exposed. This exposure of added aggregates has risen to an art form among decorative concrete contractors, and multi colored chips in concert with an appropriate overlay system becomes a terrazzo like finish. Terrazzo may be the grandmother to polished concrete, but in this type of system the overlay can become her twin sister.
Polished concrete overlays are relatively fast setting with initial set occurring within the first 20-30 minutes and final set falling directly behind at 40 minutes to 1 hour depending on temperature and humidity. Most systems reach compressive strength of 3000 PSI in 1 day and final strength within 30 days. Most polishable overlays have been engineered to mitigate down time on a floor surface and are able to be polished 24 hrs. after placement.
The Polishing Process
Concrete overlays require polishing tools and methods in keeping with the polished concrete world at large and do not require specialized tools or tooling. As with any polished concrete floor surface experienced craftsmen are the critical component to success.
While time will tell if polishable concrete overlays are the true philosopher’s stone in the decorative concrete world, at present those overlays are making significant impact. Buildings across the world are full of worn and dilapidated concrete floors. Often those floors are shrouded in layer upon layer of last year’s floor coverings. As yesterday’s floors are re-purposed for today’s uses and emerge into the light there will continue to be a growing need to figure out materials, means, and methods to return those floors to glory. Polishable concrete overlays are another arrow in the quiver of the owner and contractor alike to fight the Franken-floor monster.
Ed. Note: C.T. “Chip” Marshall is the executive vice president of Industrial Caulk and Seal Inc.. An award winning, large scale decorative concrete and concrete repair contractor, Industrial Caulk and Seal operates throughout the Mid-Atlantic and Northeast. Both Chip and Industrial Caulk and Seal can be reached through their website www.industrialcaulkandseal.com.