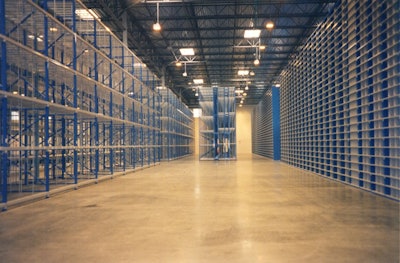
From warehouse floors to high-tech, pharmaceutical and food manufacturing facilities, the trend toward jointless floors continues to grow anywhere fewer joints, fewer cracks, less maintenance and exceptional durability are essential. Meeting this demanding performance creates challenges for concrete contractors faced with constructing a concrete floor that is both joint-free and crack-free. Since control joints are used to provide an acceptable place for concrete to crack, eliminating joints in traditional portland cement concrete is counterproductive.
Shrinkage-compensating concrete made with Type K cement enables contractors to achieve joint-free and crack-free slabs with a high-quality concrete solution. Larger placement sizes not only reduce the number of joints, but also reduce the number of mobilizations required, and minimize load transfer reinforcement requirements, helping the contractor stay on schedule and within budget.
Combating Cracks
Cracks in traditional concrete are most commonly caused by the drying shrinkage of portland cement. So, to minimize or eliminate the effects of concrete drying shrinkage, admixtures, higher quality aggregates, and various construction methods are used to try to minimize drying shrinkage cracking. Common construction methods are the use of control joints typically spaced at 15 or 18 feet, extensive rebar reinforcement, post-tensioning slab designs, and pour strips. These materials and methods are both time-consuming and costly.
%{[ data-embed-type="image" data-embed-id="58e7cf01710bfc0ef094c35e" data-embed-element="span" data-embed-size="640w" data-embed-alt="At Sofa Express, Portland, Tenn., joint spacing is up to 130 ft." data-embed-src="https://img.forconstructionpros.com/files/base/acbm/fcp/image/2017/03/SofaExpress_02__1_.58d17dfdbd25a.png?auto=format%2Ccompress&fit=max&w=1280&q=70" data-embed-caption="At Sofa Express, Portland, Tenn., joint spacing is up to 130 ft.
<br>" data-embed-width="1000" data-embed-height="750" ]}%
The Joint Dilemma
The use of tightly spaced control joints is a method of creating acceptable places for the inevitable cracks to form in portland cement concrete slabs. These joints are tooled or saw cut into the concrete after placement and then treated with joint sealant materials to prevent moisture and contaminants from entering the concrete and causing accelerated deterioration and structural failure. Properly spaced and treated control joints reduce or eliminate drying shrinkage cracking and protect the concrete from deterioration.
90-95% of floor damage in warehousing, manufacturing, and processing facilities occurs at the joints.
Unfortunately, control joints create significant challenges in concrete floor slabs subjected to repetitive use and heavy loads. Joint edges and panel corners of portland cement concrete slabs curl upward during the curing process as excess water in the slab dries out more rapidly at the surface of the concrete than the base of the slab. Curled edges leave unsupported space below the slab edges that compromise the integrity of the panel at the corners. When loads are applied from forklifts or other mobile equipment used within the facility, these weakened edges break and spall. In fact, 90 to 95 percent of floor damage in warehousing, manufacturing and processing facilities occurs at the joints.
Joint challenges not only occur in the concrete slab, but also affect the forklift equipment and equipment operators. Curled panel edges create uneven joints that generate impact forces on forklifts and other mobile facility equipment, as well as equipment operators, as they pass over the joints. Abundant joint placement means an abundance of repetitive use impact forces – on both the equipment and the operators. This ultimately results in increased maintenance and repair costs on the equipment, and health and safety concerns for operators.
By addressing joint challenges with higher quality concrete, larger slab sizes and fewer joints, construction can be simplified, time to completion of projects can be compressed, facility maintenance and repair costs can be minimized, and health and safety concerns can be reduced.
A Simpler Solution
A simpler, more cost-effective method of address drying shrinkage cracking is to improve the cement paste itself – the most essential element in concrete mix design. Type K cement (ASTM C845), based on calcium sulfoaluminate (CSA) cement technology, is designed to compensate for the shrinkage of portland cement and the aggregates used in the concrete. By using Type K cement, contractors can provide a higher quality concrete, known as Type K shrinkage-compensating concrete, which allows them to create a concrete floor slab solution that minimizes or eliminates joints and drying shrinkage cracking while reducing overall project costs.
How It Works
Type K cement is designed to create controlled expansion within the matrix of the concrete within the first 7 days. This expansion is created within the mix design using a cementitious shrinkage-compensating additive known as Komponent. The designed expansion puts the concrete in compression and the reinforcement in tension early (at the time of placement) – and overcomes the shrinkage effects of portland cement and aggregates that start to shrink almost immediately. Early tensile strengths and compressive strengths help prevent drying shrinkage cracking for the life of the placement.
Type K cement is engineered to expand by creating a strong network of ettringite crystals that: improves the dimensional stability of the concrete itself, keeps the concrete in compression throughout its designed service life, and allows much larger placements with few if any control joints.
Larger placement sizes minimize the number of mobilizations required and significantly reduces mobilization costs. Larger placement sizes and fewer joints means fewer load transfer details and reinforcement materials (e.g., dowel bars, baskets, etc.) as well. By eliminating 90% or more of the tooling, cutting and treating of control joints, additional savings is also realized. All of these aspects help minimize material and labor costs and speed time to completion of the concrete installation.
In 2004, furniture provider Sofa Express Inc. specified Type K cement for the company’s Portland, Tenn., warehouse floor. In this 70,000-square-foot installation, the number of joints was significantly reduced by extending the spacing between joints to 130 feet, rather than the 15 feet commonly used with portland cement-based concrete. Traditional reinforcement was replaced with synthetic microfiber reinforcement dosed to maximize the performance of Type K cement. The use of synthetic microfibers helped further reduce project costs without compromising durability, and allowed easy access for laser screeds to maneuver around the placement area with ease.
The project was a success. At the one year inspection, the floor flatness remained well within super flat tolerances, measuring at FF 97.8 — with no drying shrinkage cracking.
Floor System Advantages
For new construction and expansion projects that commonly face project delays and additional expenses related to grinding and leveling concrete slabs prior to installation of high-performance flooring systems and other floor coverings, Type K Cement Shrinkage-Compensating Concrete effectively bridges the gap between Division 03 (Concrete) and Division 09 (Finishes). By maintaining floor flatness and floor levelness, timely and costly delays during construction can be avoided, and floor covering installations can proceed more efficiently.
Slab Thickness Considerations
Eliminating curling and overcoming drying shrinkage affords other key advantages for slab-on-grade projects when using Type K cement. The additional slab thickness that is often designed into a slab to add weight in an effort to overcome curling can be eliminated. In addition, temperature and shrinkage steel used to try to prevent drying shrinkage cracking can be removed. Decreasing slab thickness and reducing reinforcement requirements are two additional ways Type K cement can help reduce overall project costs.
%{[ data-embed-type="image" data-embed-id="58e7cf01710bfc0ef094c360" data-embed-element="span" data-embed-size="640w" data-embed-alt="Joint spacing up to 120 ft. is found at the Costco, Mira Loma, Calif." data-embed-src="https://img.forconstructionpros.com/files/base/acbm/fcp/image/2017/03/Costco_Mira_Loma_CA_IMG_0005_2.58d17dff22068.png?auto=format%2Ccompress&fit=max&w=1280&q=70" data-embed-caption="Joint spacing up to 120 ft. is found at the Costco, Mira Loma, Calif.
<br>" data-embed-width="1600" data-embed-height="1200" ]}%
Design Flexibility
The engineered performance of Type K cement provides design flexibility for the structural engineer, designer, specifier, contractor, and owner. Whether you’re using traditional reinforcement methods, or fibers (i.e., micro-synthetic, steel) with perimeter reinforcement, Type K cement can achieve net zero shrinkage performance. This affords larger panel size placements with reduced mobilizations, and pour sequencing and panel dimensions can be modified to ensure joints are minimized are eliminated throughout the facility.
A Proven Jointless Floor Solution
Shrinkage-Compensating Concrete made with Type K cement provides a high-quality concrete floor slab that maximizes the advantages of jointless floor solutions. Type K adds value both during construction and in-service. By improving construction timelines, reducing construction costs, and reducing costly call-backs, construction teams can move forward with confidence and efficiency to complete projects on-time and within budget.
By significantly reducing repair and maintenance costs, Type K contributes to reduced lifecycle costs and improved operational efficiencies. With Type K Shrinkage-Compensating Concrete, contractors and design teams can meet and exceed owner expectations and position themselves well to secure many future project opportunities.