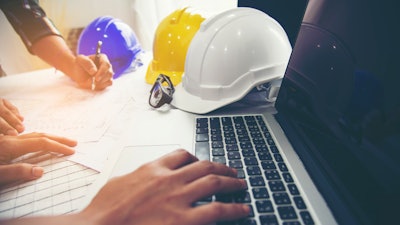
Inflation has driven the cost of everyday essentials sky-high, from food to fuel, office supplies, rent, and everything in between. Continued broken links in the supply chain and volatile construction material pricing are stretching budgets and adding significant pressure to the construction industry. How construction industry professionals overcome these financial hurdles could be the difference between success and failure in the year ahead?
Industry changes amidst Inflation
On top of rising inflation and the persistent shortage of vital construction materials, contractors and subcontractors face another threat. To combat that inflation, the Federal Reserve repeatedly raised interest rates to nearly 4%, the highest level since 2008, with more increases still under consideration. These higher interest rates are forcing significant budget cuts or can completely halt projects in their tracks. They also further impact the cost and availability of construction materials.
When breaking down a project’s budget, material costs can range from 35 to 60 percent. For the last three years, record inflation has driven up the cost of construction projects while also creating new risk management challenges for contractors. While the construction industry was able to withstand the pandemic economic slowdown better than most industries, significant barriers to success remain.
Steel cost is an example of the price volatility the construction industry has seen recently. At one point, the cost soared over 200% from March 2020 to mid-2021 before finally letting up this summer. Other critical supply costs have also risen. In fact, construction material prices have risen 16% from a year ago and 41% since the start of the pandemic. Although the industry has finally seen a decrease in supply chain bottlenecks, contractors and subcontractors continue to endure severe material cost challenges, and uncertainty abounds.
Yet another industry hurdle is the steady escalation in fuel prices. For a subcontractor with a small fleet, filling up at $3.30 a gallon could mean over $2,000 a month in out-of-pocket fuel expenses. In California, the Pacific Northwest, and parts of the eastern seaboard, fuel costs can be up to 35% higher than the national average.
Soaring diesel prices are an even greater concern for an industry reliant on heavy equipment. A recent Diesel Technology Forum report stated that 98% of all energy use in construction comes from diesel. In 2022, diesel costs rose 33% in only five weeks, sending prices skyrocketing to an all-time high of $5.78 per gallon in June. According to EIA, diesel prices have jumped 141% since the pandemic began.
Due to the nature of the industry, inflation impacts are particularly difficult for contractors and subcontractors. Inflation creates complications in cash flow, project timelines and can lead to other construction operations challenges.
On most construction projects, contractors and subcontractors must procure materials in advance and are expected to pay for those building materials within 30-60 days after purchase, long before they are paid for the job. Budget gaps will only continue to grow as those costs increase. Contractors and subcontractors lose bids and potential contracts when the cash flow necessary to float projects isn’t available.
The $1.2 trillion bipartisan infrastructure act, considered a life raft for the construction industry, has actually exacerbated challenges for the industry. Having available funding for large-scale new projects is increasing demand for already scarce materials, contributing to existing inflationary pressures. Without clear steps to help mitigate material and energy costs, prices will only continue trending upward, and contractors and subcontractors will continue to face slim margins. It’s clear to see that snowballing costs have damaging effects on the bottom line, increase the likelihood of construction delays, limit a project’s potential rate of return, and can potentially scrap projects entirely.
Asphalt & Roadbuilding Today
The infrastructure act is set to fund billions of dollars of transportation priorities, including major road and highway projects, and asphalt is the key to the success of those plans.
There are approximately 18 million tons of asphalt on America’s roads as it is the most cost-effective way to build and pave roads. The U.S. must invest in maintaining and modernizing our existing infrastructure to maximize its reliability, capacity, and performance. Our nation has built one of the world's most extensive and productive highway systems, representing billions of dollars of public and private investment. It is essential that we adequately maintain and modernize this vast, existing road system to maximize its reliability, capacity, and performance, reduce operational and replacement costs, and extend the pavement’s useful life.
According to the National Surface Transportation Policy and Revenue Study Commission of the U.S. Congress, the annual investment required by all levels of government to maintain the nation’s highways, roads, and bridges is now estimated to be $185 billion per year for the next 50 years. Today, the nation invests $68 billion, but the infrastructure act dedicates $110 billion in new spending for highways, roads, and bridges and $39.1 billion for transit programs over the next decade. This boost of funding will help launch projects across the nation but will also swallow up critical materials and limited labor. Cost increases and scarce workers could slow projects and hurt the bottom line in the near term.
Asphalt is a crucial component of building livable communities in a multitude of ways. Buses run on asphalt pavements. Asphalt underlayment helps high-speed trains stay on track. Porous asphalt can even be used to manage stormwater. Also, asphalt is a renewable, sustainable material. It is considered an environmentally friendly option. Demand for this critical material will continue to rise in 2023, particularly due to major projects funded by the infrastructure act. General contractors and subcontractors have the opportunity to significantly increase revenue but only if they have the right tools to help them find and win these projects.
Navigating change with technology
To secure potential projects, construction professionals must focus on finding solutions for what they manage. Thankfully, innovative, simple-to-use preconstruction technology can enhance control and productivity. These platforms improve planning, increase efficiency, and help general contractors, subcontractors, and suppliers collaborate more easily to establish long-lasting connections that enhance stability and success.
The technology is beneficial in the crucial bidding process. Easy access to documents and data helps create more detailed, accurate, and speedier bids. The right applications also notify construction professionals about new projects in their service area and can help them place their bids ahead of the competitors and gain an advantage.
While the construction industry is starting to prioritize the implementation of technology into its practices, it remains an “old school” business that is slow to change. Nearly 40% of specialty contractors report they still primarily use spreadsheets, whiteboards, paper-based processes, or other methods instead of construction tech platforms.
But by utilizing and leveraging the right construction planning and management solutions, contractors and subcontractors can view important information crucial to potential or ongoing projects digitally instead of sifting through old bidding documents, spreadsheets, and random notes. Software solutions provide quick and easy document replication, streamline bidding and other vital processes, and save businesses time and money.
Digital solutions can help contractors and subcontractors save money, maximize efficiencies, and mitigate the adverse effects of inflation. By prioritizing innovative construction planning and management technology today, construction professionals can improve critical business functions, strengthen collaboration, and be better prepared for the myriad challenges awaiting them in 2023.