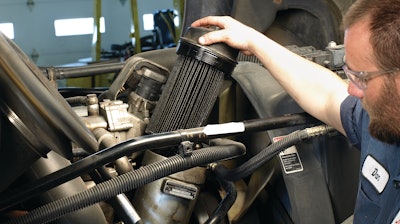
The lube system in an engine functions as its central circulatory system. It keeps engines running at top performance by lubricating, cooling and cleaning the engine through the entire oil drain interval.
Monitoring oil quality through the implementation of a regular oil analysis program can help identify potential engine issues before they happen, or worse yet, before they progress to larger engine issues. An oil analysis program forms a solid, data-driven foundation to help you optimize preventive maintenance practices for your heavy-equipment fleets.
Effective analysis and PM optimization can lead to:
- Less unplanned downtime through identifying minor problems before they become major failures
- Reduced overall cost of lubricants by safely optimizing drain intervals
- Identifying opportunities for optimizing filtration performance
- Maximized asset reliability and extended equipment life
Common contaminants
As contaminant levels increase, engine wear increases. In modern diesel engines, there are several types of contaminants that do not belong in engine oil:
Ingested dirt, which can enter the engine through the air intake system, a failed engine gasket, or a contaminated fuel supply. It appears primarily in the form of silica.
Wear metal, which is the product ofAn oil analysis summarizes the condition of engine oil and identifies component wear/contamination. It typically includes evaluating the test results and providing detailed reports, including maintenance recommendations. It’s a fast and highly accurate way to assess what’s going on inside your engines. Equipment owners use the data and recommendations to improve preventive maintenance, reduce equipment downtime, and reduce costs by extending oil drain intervals.Donaldson Company
Soot, or the byproduct of partially burnt fuel. Excessive soot is a sign of reduced combustion efficiency. Soot is introduced into engine oil by operating an engine in a gear that’s too high, improper timing, intake or exhaust restrictions, or by engine idling. In newer emission-compliant engines, soot can increase from blow-by gases and EGR (exhaust gas recirculation) systems. As oil degrades, soot can agglomerate and increase wear. Excessive soot also adversely affects oil viscosity. Since the introduction of EGR, soot levels in some engines can be the limiting factor in oil change intervals, because soot levels in the oil have increased in some engine configurations.
Fuel in oil is a problem caused by factors such as worn injectors, a line leak, plugged air filter, or improper timing. Fuel in oil will thin the oil, reduce oil pressure and allow harmful metal-to-metal contact. Excessive fuel in the oil can have even more catastrophic consequences.
Water is produced by combustion and usually carried away with the exhaust. In cold engines, however, water can condense in the crankcase. Water can also be ingested when adding oil. Water in engine oil decreases lubricity, prevents additives from working effectively, facilitates oxidation and promotes acid production, which can lead to corrosion and wear.
Coolant in the form of glycol/water contamination can enter engine oil through a bad seal, pitted liners, a cracked head, an engine block water pump, or an EGR cooler leak. On engines with EGR, the exhaust gases need to be cooled before being reintroduced into the combustion chamber. This is accomplished by the use of an EGR cooler, which uses coolant to reduce the temperature of exhaust gases. Coolant in engine oil causes glycol sludge, which plugs oil lines and filters, and causes rapid additive depletion.
Why routine oil analysis is so important
Routine analysis of engine oil provides the necessary information for effective preventive maintenance. It is a fast and highly accurate way to assess what’s going on inside engines. It summarizes the condition of the oil and identifies component wear or contamination.
The chemistry and concentration of wear metals can allow a skilled person to identify the probable root cause of contamination, such as the engine component that may have led to the above-normal presence of the wear metal in engine oil. For example, the presence of sodium or potassium in engine oil can be a strong indicator of glycol (coolant) in the engine oil. A high total acidity number (TAN) can be an indication of corrosion of metallic components, accelerated components wear, or an oil-drain interval that’s too long.
Often, oil analysis programs run throughout the life of an engine, thus giving a unique indication, or chemical signature, of the engine’s entire history. With that in mind, it is essential to review the entire log of oil analysis reports to reach a conclusion about what is happening within an engine. To illustrate, high but stable amounts of boron could indicate dispersants or oxidation inhibitors, while consistently increasing amounts could indicate a coolant leak.
The filter's job just got harder
To fulfill their role of protecting engines, lube filters need to capture wear metals, soot and other contaminants from the engine oil. In order to maintain the higher oil cleanliness standards required by today’s most advanced engines, lube filters must work harder than ever before.
With the introduction of FA-4In order to maintain the higher oil cleanliness standards required by today’s most advanced engines, lube filters must work harder than ever before.Donaldson Company
The secret is balancing the three characteristics of filter performance:
- Efficiency, which refers to a filter’s ability to remove contaminants at a given particle size
- Capacity, which is the amount of contaminant (measured in grams) that a filter will hold before the restriction exceeds recommended limits
- Restriction, which refers to the amount of pressure loss between the upstream and downstream sides of the filter (often characterized as pressure drop).
For lube filters, the secret to balancing all three characteristics is hidden underneath the surface of the filter. With the introduction of EPA 2010 regulations for the on-road market and Tier 4 regulations for the off-road market, some equipment manufacturers chose to control lube oil contamination at finer levels than before, which led to the development of newer grades of synthetic lube filter media.
Filtration suppliers are continuing to push the limits on newer technologies that offer tighter control on efficiency with reduced pore size, and they can deliver high contaminant capture for less engine wear, less flow restriction for better oil flow, and more contaminant holding capacity that can extend filter service life. These characteristics all support extended oil-drain intervals and lower operating costs for customers who need filters to support extended-maintenance programs.
Tips on extending oil-drain intervals
If fleet managers choose to extend intervals, they need to start carefully and incrementally collaborating with oil and filter suppliers by conducting oil analysis at each newly extended interval, and by inspecting filters for any signs of issues. If an interval is extended too far where the oil loses its lubricating properties, it can cause accelerated engine wear. It can also stress the filter to the point that it damages the filter or degrades its performance. In the end, this will impact engine performance and efficiency.
Although fleets may have their own sampling practices set by the engine or vehicle manufacturer, if they are not available, a general guideline is to sample the oil every 10,000 miles for on-road diesel engines, and 250 hours for off-road diesel engines. Although oil sampled from an engine does not “break down,” any lengthy delay between sampling and analysis can be crucial if a unit is failing, and thus should be avoided.
Because engines, operating conditions, oils and additives can vary, it is highly recommended to have a comprehensive extended-maintenance plan that includes ongoing oil analysis as part of any extended-drain plan. Working with a reputable filtration supplier and utilizing an oil analysis program is the best way a fleet manager can ensure they have the proper filtration in place to meet the demands of their fleet. It is essential that equipment owners collaborate with their oil and filter suppliers to analyze and draw meaningful conclusions from the data captured.