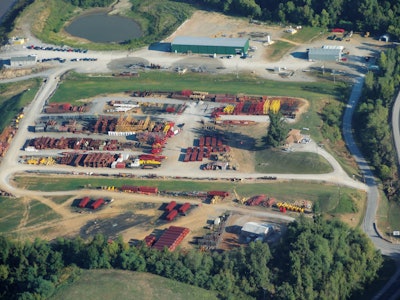
Certified Equipment Manager Mason Ford doesn’t like equipment storage yards. “I don’t know that there is truly a benefit, with the exception of specialized equipment such as specialty fabricated items—power cranes, floating rigs, tunnel boring machines that type of thing,” Ford says. “I do the math pretty regularly. If it’s less expense to store, we hold on to it for a couple of months and then get rid of it.”
Ford’s philosophy is based on the nature of the business he is in. He is director of equipment for Skanska USA, a business unit of Skanska AB, which is a major construction and development company. He is directly responsible for the $500 million fleet of mostly off-highway equipment that focuses on operating units to fit a project that is in progress, rather than storing machines and material for projects already completed.
Unlike a company that is, for instance, in the airport business and keeps concrete equipment in storage yards around the country, “we are project-centered,” says Ford. “Our fleet is maintained mostly for projects, not for work types or regions. Seasonal work is not typically for us except in our industrial division. Currently, we are not doing a lot of recurring business.”
The idea that storage with the intent of using the equipment later is cheaper than alternatively buying equipment when you need it “typically is just not true,” Ford says. “I am a big advocate of not having storage yards, but if you do have them, you have to maintain the stuff you have in the yard. You have to handle it, and for anything long-term, I believe it is always better to liquidate and have less overhead.
“If we (the industry) had to make a business case on the value of storage every time you keep something, as we do when we make acquisitions, people would make a different decision,” he says. “People would store a lot less stuff.”
Storage site selection and management
Maintaining the yard, Ford says, means anything from having the correct fluids to handle a freeze, to protection against rats, mice, snakes, birds, insects and other threats. “They can attack equipment, and the one thing you don’t want is to come back and find a fleet of equipment that contains beehives or bird nests,” he says. “They can do real damage to wiring and lights. It’s not uncommon to come back from a break and find a machine has electrical problems because mice have eaten all the insulation off the wiring.”
Within that framework, Ford considers certain factors in selecting a storage site, such as the five-acre property the company maintains in New York City. Ford suggests a location with good access and good storage for temporary items, such as heavy equipment.
“We also store some of the permanent materials that go into the project and heavy equipment, for instance, that would be used immediately after the project,” he says. “We don’t store anything permanently, except beams or fabricated trestles and project-executed items for our industrial business. We don’t like things sitting around.
“Yellow iron, like cranes and excavators, will be stored if we have a place to use them and if we’ve done the math and determined that is the best formula for keeping it rather than disposing of it. If I have equipment 'sitting around', then I store them with a dealer, even to turn them sometimes.”
Storage yard tips
When setting up a storage yard, keep these guidelines in mind:
- Store equipment so you can start the engine at least once a year
- Store the equipment facing forward toward the roadway, so you don’t have to get out and walk around the unit for identification numbers needed for inventory
- Store equipment off the ground by placing it on ground-level foundations such as cross ties or treated lumber
- Shrink-wrap equipment to avoid having to take it inside.
Hidden costs of storage
“Another storage cost is rooted in human nature,” Ford says. “People want to keep everything. Yet another hidden cost is that you are tying up opportunities for the yard’s square footage. Our prime, five acres of real estate in New York City, which is worth approximately $50 million, could be rented for about $100 per square foot. The value of anything stored there needs to be compared to the alternative space value.”
There is also the opportunity to earn interest on money not tied up in owning equipment—“but that is a whole different topic,” he says.
Ford’s operation is different when it comes to choosing a site because much of his work is urban. We go with what is available,” he says. “Many times, we use the property of the owner of the particular project. We incorporate that within the project.”
Although Ford operates with a don’t-store philosophy, projects themselves sometimes force the decision.
Thad Pirtle, CEM, vice president and equipment manager, Traylor Bros., has an outlook similar to Ford’s. “When it comes to deciding whether to keep or dispose of equipment, it depends on your needs,” he says.
“If we have another job coming up within a year in the same area, we will store, for example, locomotive engines or other things you can’t buy off the shelf,” Pirtle says. “If we have a project that is coming up in a year or two, we will buy a yard and store what we need into that yard to get a head start on the future project.”
Deciding what equipment to keep and what to dispose of may be a gray area. Traylor Bros. usually sells conventional equipment, such as loaders and dozers, but specialty equipment is a tougher call, Pirtle says. “Are we going to keep it five years, 10 years, or until it is antiquated and then get rid of it?”
If equipment is going to be stored, certain factors have to come into play. “Hydraulic cylinders, for example, have to be coated with some kind of protective oil or grease so they don’t rust,” Pirtle says. “Engines should have long-life coolant, so we test coolant annually, the same as an operating machine. Stored engines also are started at least once a year. You treat them just like you do a boat when you are storing it.”
When Pirtle chooses a storage yard, he looks for a location near the place he plans to be coming and going or near a working yard. Another consideration is to select a site where you are going to work for several years.
“If we are going to be on a job in California for a long time, we use a yard we have in or close to Los Angeles. If we have another job coming up in the same area, we also store the equipment for the upcoming job,” Pirtle says.
The most important consideration of all is to make sure the site has security against vandalism, he says. “Also, you must have good drainage and a fence all the way around the yard.”
The best guideline is to store everything inside a structure, not let it sit outside in rain, heat, cold, and other climate conditions—not to mention vulnerable to insects, rodents, birds, bees and groundhogs. “Varmints are always a problem,” he says.
Pirtle treats outside storage for larger machines differently.
“We shrink-wrap them and keep them off the ground by using cross ties—which are expensive, but worth it— and treated lumber. The railroad ties are placed between the ground and material, then the treated lumber is utilized above the ground,” Pirtle says. “Other outside storage items might be wire ropes or boom sections.”
LPR Construction, a Colorado-based company with roots in steel erection and now expanding into industrial and millwright work, also needs to store smaller items other than machines. Thad M. Lutgens, LPR’s director of equipment and IT, is responsible for about 80 vehicles, multiple welder stations, ironworking equipment, millwright, concrete, and pipe fitting tools.
“Oftentimes we rent, due to the number of out-of-state projects we are involved in,” he says. We own many of our smaller pieces, which are easier to transport across the country. During slow periods, we can ship the smaller equipment back to our headquarters, which is much more cost effective.”
Since projects use much of the same type of equipment, Lutgens says keeping it outweighs the cost of acquiring new. “If there is life left in the equipment,” he says, “we hold on to it.”
An example of equipment that would be kept and shipped back is a tension control bolt electric shear wrench, a specialized iron-working device that tightens a nut on a bolt when erecting steel. when tightening reaches the correct, specified point, the tool snaps off the tip of the bolt.
“That piece of equipment is small enough to meet our four measures of value,” Lutgens says. Does the value of the tool meet our threshold? Is it small enough to ship if needed? Is it something we can utilize time and time again? And how much productive life is left in it?”
Because the company does a lot of structural welding, it has about 27 welders and wire feeders. Some are owned while others are leased. “This equipment is shipped back since they are special pieces of equipment that cost about $2,500 each and are used on nearly all of our projects,” he says.
When large items are involved, Lutgens says, they consider shipping cost, its value, and whether it is a specialized piece of equipment that can be used over and over again and can be easily shipped.
“We’ve purchased some specialty equipment that is extremely heavy, so we have to figure out if we want to dispose of it or keep it for the next go-around,” he says.
Selecting a good storage area for such units is always a challenge, Lutgens says. LPR construction may coordinate with the contractors or the workers to arrange a boneyard.
“That is where we store a lot of our materials,” he says. “We partner with the general contractor, and while the project is being built, we store equipment as well as building materials on that site.”
Although not frequently, Lutgens has run into situations where the boneyard space is so tight he has to go outside the work perimeter and use space that has been a storage site. Sometimes the space is a mile or mile and a half away from the project.
Joint-venture considerations
Joint-venture projects pose specific challenges. “You have to be very, very careful to identify what is your equipment and what is your partner’s equipment,” Lutgens says. “Any equipment you put on site must be clearly identified. Otherwise, it becomes a massive project to sort out whose is what.”
A pause in a long-term project also poses storage problems, and Lutgens cites this example.
“The project has three units, and they wanted to complete each unit fully before proceeding to the next,” he says. “Our piece was a small component of the entire project. We completed our work in the October-November time frame. That’s where we paused. We stored our equipment on site for three months in a weatherproof storage box.” Lutgens also stresses the importance of preparing equipment and materials for storage.
“Obviously, you need to know what tools are in your inventory and fully document your entire arsenal you put in storage,” he says. “When units come back to our yard here, they go through a check-in process. We use software that allows us to scan the item and place the information into our system, letting us know its location and availability.”
The actual storage space depends on what you are storing. Sensitive electrical equipment has to be protected from the weather and placed in a controlled environment. In Lutgens’ case, the environment is a semi-tractor trailer(s). “You don’t want any surprises when you go to get it,” he says.
Lutgens doesn’t use any seasonal yards, but he says the main difference between them and long-term yards is that seasonal yards are temporary and used for anything “you can pack up, walk away from, and know you are not going to need for the next six months.”
Long-term storage yards, by comparison, require a full-time staff to manage them. They monitor what’s coming in and out, along with being there when someone needs the equipment.
Lutgens adds that it helps to have a good relationship and strong communication with the operations staff, superintendents, and project managers.
“If you don’t have them on board,” Lutgens says, “your life is going to be a lot more difficult.”