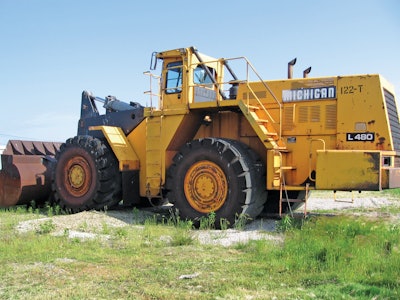
Congratulations, you’ve got a new job! With this position you’ve inherited an aging fleet; a host of maintenance sins from the past; limits in maintenance personnel, repair facility capabilities, and your capital budget; and, of course, an operational budget that is stressed and strained due to the facility's past financial performance. Welcome to the Big Leagues.
This is a scenario many of us have had to work through during our fleet management careers. When facing a situation like this, my suggestion is to develop a strategy based on your location’s asset issues, and provide local maintenance leadership with the ability to implement a plan that meets your strategy.
Prioritize fleet assets
To create that strategy, you first need to prioritize your fleet assets. Not all assets are created equal. Identify the assets that are important to the success of the operations. Your limited capital and operating budgets should be utilized to make sure these assets are “operation ready.”
Define your assets in terms of how essential they are to operations, and if there are alternatives for replacement should the assets fail. For example, prioritize assets with significant commercial, operational, or environmental impacts, and those with very limited alternatives for replacement. These are your Category 1 assets. Category 1 assets are your priority because if they fail, your operations may screech to a halt.
Category 2 assets are those used in day-to-day operations. They may impact operational capability, but you have some alternative means of executing business if they are not operational.
Category 3 assets have minimal, or no impact, on regular operations.
Note that the category for each asset may change from year to year, depending on the demands from operations. Review your asset categories annually to be sure they line up with actual operational needs.
Devise a backup plan and repair matrix
Next, your strategy should include a backup plan. What happens if your top asset is down? These assets are often difficult to repair or replace in a timely fashion. Develop a plan now that can be implemented at a moment’s notice, and by anyone in the maintenance department, before it becomes a problem.
Now you can develop a repair matrix based on the ability of maintenance staff and your facility’s capabilities. Is your maintenance staff working on issues that are difficult to complete based upon the number of technicians, the tools required, or limited space in the shop? Are they working on the assets that will provide operational success?
Line up support, improve internal communications
Once you have prioritized your fleet’s assets, and developed your repair matrix, you can identify areas where you need outside vendor support. Be proactive and identify vendors who can provide the support you need. Build relationships and make agreements with them (with terms and conditions on file) for a service program covering on-site work and an after-hours program. Don’t wait until an emergency has developed to start this process.
Your strategy’s success hinges on clear and regular communication between your maintenance department and operations. Schedule weekly discussions on asset requirements from both the operations and maintenance perspective. If your maintenance team knows the demands of its customers, and operations understands the maintenance department's requirements, there should be no surprises.
A key element in communication between maintenance and operations is the status of your Category 1 assets. Maintenance and operations need to be in constant communication with each other about the following:
- Are your Category 1 assets capable of handling the required application for operations?
- Which Category 1 assets will need repairs to keep the machine operable for the required application?
- Have minor repairs been added to the next scheduled maintenance service?
- Is there a Safety Down issue where the asset is not available until inspected by maintenance? When will it be approved by management to return to service?
- Is the asset subject to a work order and not available due to repairs to be completed in the next 24 hours?
- Is the asset on a Hard Down order and not available due to a major report or safety issue keeping the asset unavailable for more than 24 hours?
- Is this information important to operations?
Operations and maintenance should work together. Operators must be trained to complete thorough pre-use inspections and inform maintenance of any issues they find. Equally important is the maintenance group’s response to promptly let operations know the items they've identified have been reviewed and a repair plan developed.
Finally, you need to understand the total capital dollars available for your organization. There are never enough CAPX dollars, so you must prioritize your spending for assets that have the greatest impact on your operation's financial success. Look for ways to stretch your CAPX dollars. For example, consider refurbishing or rebuilding assets; leasing equipment or a lease buyout; rental purchase options; or purchasing used equipment. Consider expansion capital for new business. There could be some potential for excess expansion capital dollars used for replacing or improving your existing assets.
Remember, an aging fleet that has not been maintained with a proper level of care did not happen overnight. Without an effective strategy in place, your focus will jump from one fire to the next, causing frustration for operations and maintenance departments, as well as your customers.
By developing a strategy that prioritizes your assets, you can begin to work with the maintenance team, your vendors, and operations to implement a plan that, over time, will increase the productivity of your assets and improve the financial performance of your operations.