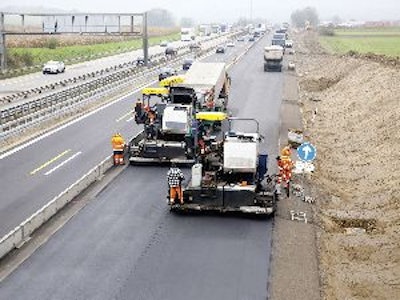
The expansion of the A 9 Federal Motorway to the north of Munich was a special job in many respects. Contractor Richard Schulz Tiefbau GmbH & Co. KG rehabilitated the surface course of a motorway section, involving three lanes and a temporary hard shoulder, by placing a thin overlay. What's more, the mix used for this job has special noise-absorbing properties. This innovative surfacing was paved "hot on hot" with two SUPER 1800-2 pavers equipped with SprayJet Module.
The A 9 motorway is one of Bavaria's most important long-distance traffic arteries, linking the two cities of Munich and Nuremberg. A considerable share of the traffic between northern and southern Europe also flows on the six-lane motorway.
On average, some 97,000 vehicles use the A 9 every day, including some 11,000 heavy goods vehicles. When the daily average is exceeded, such as on Fridays and Mondays due to commuters, or during holiday seasons, there are backups stretching for kilometers.
In the medium term, tight public budgets made it impossible to comply with the wishes of many car drivers to expand the A 9 to 8 lanes. So instead, the Highway Authority of Southern Bavaria came up with a creative solution: using the hard shoulders during the morning and evening rush hours to absorb the peak loads in future. This would effectively provide an additional lane in each direction without incurring major costs.
Expansion of the motorway on a 6km section
The first phase of the project involved expansion of a 6km stretch in the direction of Nuremberg, starting to the north of the Neufahrn junction, just shy of 20km from Munich. One condition imposed by the contracting authority was that three strips in each direction were to remain open during the roadworks, with one strip in each direction being re-routed to the opposite carriageway. The paving teams thus had to work with ongoing traffic.
Temporarily opening the hard shoulders to traffic was easier said than done, as the pavements are not designed for the loads exerted by heavy goods traffic. So the hard shoulders had to be reconstructed. All of the old asphalt pavement was removed down to the anti-freeze layer and subsequently built back up to the binder course. New emergency stop bays were also added, in order to minimize the risk of a vehicle breaking down on one of the regular lanes.
For the three regular lanes, only the surface course and binder course were milled out. Here, too, the paving team of contractor Richard Schulz GmbH & Co. KG renewed the binder course, laying the basis for paving a thin overlay on spray seal, hot on hot, across the entire width of all three lanes.
Pavers with sprayers get to work
Once these preparations were finished, it was time for two SUPER 1800-2 with SprayJet Module to go to work paving the thin overlay on spray seal, hot on hot (DSH-V). All told, the jobsite was 15.2m wide. The overall width was split into two strips of 7.6m each, and each of the two VÖGELE pavers operated in spray mode across a pave width of 3.8m.
The two machines had to be perfectly coordinated. After all, the goal was to complete the paving job as smoothly as possible. A VÖGELE MT 1000-1 Mobile Feeder thus assisted in supplying mix to one of the two pavers.
The paver operators from contractor Richard Schulz GmbH & Co. KG approached the job with great concentration and a certain degree of apprehension. But before long, they were visibly more relaxed, primarily because the SUPER 1800-2 spray paver is just as easy to operate as a "normal" VÖGELE paver. The spray paver also comes with the ErgoPlus operating system. In contrast to the conventional SUPER 1800-2 without SprayJet Module, this machine is equipped with an emulsion tank on the right-hand side, as well as an extra operating console for the spray functions.
Grade and slope sensors were not required when paving the 1.5cm overlay. The self-leveling properties of the SUPER pavers with their AB 500-2 Extending Screeds contributed to the perfect evenness of the new surfacing.
Use of noise-absorbing asphalt
The numerous backups on the A 9 were not the only reason for expanding this stretch of motorway. The motorway runs through a densely populated area and traffic noise was a nuisance to many of the local residents. That was why a special noise-absorbing asphalt was to be used for the surface course across the full width of the motorway.
The mix responsible for the sound damping effect is a special material for thin overlays known as DSH-V (0/5) with PmB 65 (70/100) polymer-modified bitumen. This material is characterized by a high content of double broken and double screened chippings and sand, which results in a sufficiently high voids content in the finished layer, allowing a share of the sound waves to be absorbed. In combination with the PmB 65 (currently: 45/80-50) binder, the DSH-V (0/5) material is able to withstanding the heaviest traffic loads.
The two SUPER 1800-2 with SprayJet Module applied emulsion (type C67) and paved asphalt in a single pass. The rate of spread for the emulsion was 800g/m2, thus ensuring reliable interlocking of layers.