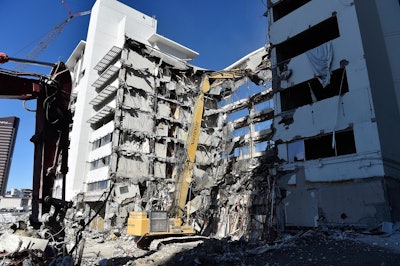
By Alexa Schlosser
Information from this article was first published in Demolition Magazine and is being reused with permission from the National Demolition Association.
Even if you’ve never been to Las Vegas, you’ve likely seen the Riviera Hotel and Casino. Portions of the James Bond film “Diamonds Are Forever,” the mob classic “Casino” and the latest Jason Bourne movie, among others, were filmed in the Las Vegas Strip’s famous first high-rise hotel.
But after 60 years, the bright lights of this Sin City destination have been switched off. “The Riv,” as it was known, closed in May 2015 to make way for an expansion of the Las Vegas Convention Center. In 2016, NDA members NorthStar Contracting Group and Controlled Demolition Inc. worked together to demolish and implode, respectively, the 20 significant structures that made up the 26-acre Riviera campus.
Four total buildings were imploded, including the Monaco Tower, Monte Carlo Tower, South Tower and South Tower expansion. Other buildings demolished during the project include the east warehouse building, east garage, west garage, east pylon sign, convention building, convention expansion building, cafe and low-rise pool buildings, central plant, San Remo Tower, lobby structure, paint shop building, Versailles Theater, North Casino, North Casino expansion, North Tower and Beckett Tower.
Interior methods
The project officially kicked off on April 18, 2016, with NorthStar performing the removal of other hazardous materials (OHMs), including PCB ballasts, mercury light tubes, neon, spent printer toner and inks, paints, solvents, cleaning supplies, e-waste, compressed gasses, fuels and oils. All OHMs were systematically collected by NorthStar-trained personnel using the proper personal protective equipment. These materials were then properly packaged, manifested and disposed of in accordance with federal, state and local laws and regulations.
Following OHM removal, NorthStar conducted asbestos abatement activities using its experienced asbestos abatement personnel. NorthStar ensures that all abatement personnel have current training, physicals and respirator fit documents. Controlled access zones (CAZs) were constructed to demarcate the asbestos abatement work areas. These work areas utilized the proper engineering controls, such as containments, for the various types of asbestos-containing materials being removed.
All asbestos removal activities were conducted using wet methods with amended water, and the asbestos waste material was bagged or containerized on the levels/floors of the building from where it was generated. The containers of asbestos waste were placed in tub carts and transported down the existing elevators, then placed into the lockable roll-off containers for off-site transport to the approved landfill. All asbestos waste was properly labeled, documented and disposed of.
Following OHM and asbestos abatement, the soft demolition of existing tenant improvements began. This work was conducted using NorthStar trained personnel and skid steers. NorthStar’s structural engineer, Sigma Engineering Solutions Inc., provided the floor-loading calculations and requirements to ensure the properly sized skid steer was used in each hotel tower or elevated floor above the slab on grade.
NorthStar uses wet methods for dust suppression, utilizing hoses and misting devises. CAZs were set up on the active levels of the hotel towers or casino areas, restricting access during demolition activities. Skid steers demolished the walls, ceilings, floor coverings and MEPs then transported the construction debris to the drop zone CAZ. The drop zone CAZ is where demolished debris is conveyed to ground level where a debris staging yard was set up at the interior pool courtyard.
This courtyard area was its own CAZ, where access was controlled by the use of fencing, banner tape and signage to demarcate the area. In this zone, the demolition debris was then loaded into dump trucks for transport to the landfill. Water misting devices were used for dust control during the debris loadout activities.
Exterior methods
NorthStar’s conventional demolition methods were used on all structures other than the hotel towers — Monaco, Monte Carlo, South Tower and South Tower expansion — that were scheduled for implosion. Once the selected section of the building was cleared of all soft debris, the CAZ was demarcated and the mass demolition process began on the selected Riviera building structures.
Demolition was performed using techniques that allow for the easy segregation of waste/debris types. The majority of the demolition was performed using hydraulic excavators equipped with cutting shears and grapplers as attachments. NorthStar anticipated using as many as two excavators per team and four teams total, operating concurrently while the large-scale demolition and waste-sorting activities were underway.
One or two of these excavators utilized a combination of shear/crusher/breaker/stinger attachments to dismantle the building and shear the steel beams. The remaining excavators were equipped with grapple attachments to handle and load the waste into trucks for off-site disposal.
By NorthStar utilizing the excavator-mounted attachments, the demolition/dismantling work was performed safely, efficiently and selectively. Roof sections were cut and removed with the shear or stinger attachments. Upon exposing the beams, the shear would remove the beams and segregate the steel or concrete and roof panels from the structure.
The exterior walls were dismantled using the grapple attachments on the excavators, and concrete walls were removed using a breaker attachment. The concrete debris was properly sized and stockpiled for on-site crushing and subsequent reuse as fill material. These structures had their foundations excavated and removed to 5 feet below grade, with the exception of the basements, where the slabs on grade and foundations beneath remained.
Implosion methods
Controlled Demolition Inc. performed Phase I of the implosion — Monaco Tower — on June 14, 2016. Fifteen crew members were utilized for preparation and explosives handling operations. Explosives were placed in the basement, first, second, fifth, eighth, 11th, 14th, 17th and 20th floors. The total duration of the implosion, from “fire” to debris settling, was 20 seconds.
Phase II of the implosion — Monte Carlo Tower, South Tower and South Tower expansion with marquee — was performed on August 16, 2016, utilizing 10 crew members. It took 19 seconds and 2,725 pounds of explosives to bring them down.