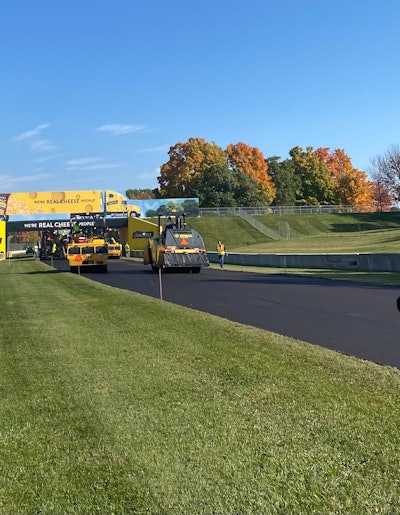
Service and maintenance vehicles, as well as construction equipment, are musts on any construction site, and staying safe around those vehicles is of utmost importance for both civilians and construction workers.
The U.S. Bureau of Labor Statistics indicates that in 2021, the construction and extraction industry had 951 fatal work injuries, of which 370 occurred as a result of falls, slips and trips and 152 due to contact with objects and equipment. The industry sector is ranked among the highest for such injuries.
As stated in a ‘Toolbox Talk’ from the CPWR-The Center for Construction Research and Training, not only does properly maintaining, repairing, cleaning, and storing construction equipment help prevent injuries and deaths, it also makes the equipment last longer.
Equipment should always be inspected to ensure it is in safe working order and good repair. Damaged equipment should never be used, and a supervisor should be alerted if equipment needs to be maintained, cleaned, or repaired.
Proper lockout/tagout procedures should be conducted to control all hazardous energy sources before maintaining, cleaning, or repairing equipment.
The same safety rules applied to all equipment to protect workers and civilians who are near the equipment also applies to service and maintenance vehicles.
Although it didn’t focus solely on accidents around maintenance vehicles, a 2022 CPWR survey, ‘Struck-by Hazards, Barriers, and Opportunities in the Construction Industry’, indicated that struck-by incidents involving an object forcibly impacting a person are a leading cause of construction industry fatal and nonfatal injuries.
Most of those who answered the survey were employed by a contractor in commercial construction.
Survey participants identified the primary causes of struck-by incidents as working around heavy equipment or vehicles (35.6%) and falling/flying objects from heights (29.8%) or on the same level (18.8%), and motor vehicle intrusions into the workspace (8.2%), among others.
One notable result involved barriers to prevention: a lack of understanding of the hazards, time constraints caused by scheduling pressures or an emphasis on production, and a lack of training on hazard identification and prevention.
Suggested protective measures include training workers on struck-by hazards, restricting access to work areas, utilizing spotters, and using back-up alarms and signals, and personal protective equipment (PPE).
Planning also is considered critical, such as conducting a job hazard analysis as well as disseminating information like toolbox talks, reminders, prompts and posters.
Just as important as workers and civilians staying safe around service and maintenance vehicles, so too is it critical for the service vehicle drivers themselves to help maintain safety, especially in cold climates with snowstorms and blizzards, but also throughout other seasonal hazards like rain and windy conditions.
Custom Truck One Source offers several tips for doing so, incluing dressing in high-visibility work clothes and wearing waterproof boots with optimal traction. Having basic emergency supplies on hand such as a first aid kit is critical, as well as winter emergency supplies such as food, water and a blanket. Wearing a seat belt is crucial, even and especially for operators who must constantly enter and exit the vehicle.
The maintenance vehicle itself also should be maintained properly. That means ensuring tires have no wear and tear as to compromise traction on icy roads and that the vehicle has a spare tire in good condition.
It’s important to be up to date on key maintenance factors such as the engine, coolants, battery and brakes. Lights should be in optimal working condition and clear of ice and snow as to provide crucial visibility. Tow trucks fittings should be properly greased.
In driving the maintenance vehicles, right-of-way should be given to snowplows and sanding trucks. Vehicle operators should keep vigilant for black ice and not engage the jake brake on icy roads.
Keeping a safe driving distance and avoiding traveling as part of a pack or following taillights of the vehicle ahead also is recommended.
An American Road and Transportation Builders Association training program on preventing runovers and back-overs in roadway work zones for the U.S. Centers for Disease Control (CDC) and Prevention and the National Institute for Occupational Safety and Health (NIOSH) can be found at https://www.osha.gov/sites/default/files/2018-12/fy11_sh-22285-11_InstructorInfo.pdf . It offers a multitude of suggestions for ensuring safety.
The Federal Highway Administration’s Manual on Uniform Traffic Control Devices offers fundamental principles of temporary traffic control (TTC), which focuses on the safety of road users traveling through the temporary and constantly changing conditions unexpected by the road user.
Equipment and vehicles moving within the activity area create a risk to workers on foot. The separation of moving equipment and construction vehicles from workers on foot provides vehicle operators a greater separation clearance. The division between moving equipment and workers on foot also improves sight lines to minimize exposure to moving vehicles and equipment hazards.
A well-executed TTC plan includes worker training on how to work next to motor vehicle traffic in a way that minimizes their vulnerability. The use of temporary traffic barriers along the workspace depends on factors such as lateral clearance of workers from adjacent traffic, traffic speed, duration and type of operations, time of day, and traffic volume.
Speed reduction is another consideration in considering the use of uniformed law enforcement officer or flaggers to help reduce the speed of vehicular traffic mainly through regulatory speed zoning, funneling, and lane reduction.
The internal activity area should be planned to minimize back-up maneuvers of construction vehicles and reduce risk exposure.
Worker safety planning is another factor, with a trained person designated by the employer conducting a basic hazard assessment for the worksite and job classifications required in the activity area. The safety professional determines whether engineering, administrative, or personal protection measures should be implemented.
A Temporary Traffic Control Plan (TTCP) describes how a specific work zone is to be set up to ensure the safety of the motoring public, central to the safety strategy of construction workers. But equipment and vehicles within the workspace require an Internal Traffic Control Plan (ITCP) and pose the hazards ITCPs are designed to mitigate.
An ITCP involves coordination of construction traffic inside the activity area of a temporary traffic control zone with its purpose to separate to the greatest extent possible construction vehicles and equipment from workers on foot.
TTCPs and ITCPs contain common principles, including providing clear direction to drivers, separating moving vehicles from workers on foot, using temporary traffic control devices to mark traffic paths, and maintaining a smooth traffic flow.
Steps in an ITCP include reviewing contract documents and model plans, determining the construction sequence, drawing the basic work area, plotting pedestrian and vehicle paths, locating utilities, considering storage and staging areas, preparing ITCP notes, and developing a communications plan.
ITCPs create ‘zones’ designed to minimize interaction between workers on foot and construction vehicles by designating routes and operating procedures for large trucks delivering materials. The plan also creates a traffic pattern to minimize backing. This is one of key elements of the ITCP as backing is the greatest hazard for workers on foot. Many state laws provide helpful guidance in this regard.
One of the driving factors is blind spots (or blind areas). A blind spot is the area around a vehicle or piece of construction equipment that is not visible to the operator, either by direct line-of-sight or indirectly by use of internal and external mirrors.
Basic actions workers can take to avoid hazardous blind spots include not crossing directly in front of, immediately behind or near vehicles.
There should be communication with a truck operator verbally and/or by a confirming signal before entering any area near the vehicle.
If workers are required to be near parked equipment or trucks, they should stand in front or on an operator’s side so if equipment comes into use, the operator can see them, and they can see the operator.
NIOSH points out in its document that consideration needs to be given to human habits and behaviors of workers on foot when developing an ITCP plan, including such factors as where workers congregate such as during weather extremes, bathroom locations, and safe walking routes from one point to another.
The plan also should take into consideration how cell phones and radios are used.
Worker visibility is key and should consider high-visibility garments meeting industry standards for work functions.
Backing safety takes into consideration that the work area should be organized to minimize backing, backing should only take place in designated locations and that there should be clear communication between the operator and workers on foot before backing begins.
Additionally, operators should be certain of their surroundings and the location of workers, equipment and ground obstacles, the NIOSH document points out. Spotters should be identified and used when possible and practical, especially when backing or maneuvering near workers on foot or other hazardous conditions.
All workers should be trained to avoid approaching or working near backing equipment. Operators and drivers should avoid backing up unless necessary. Operators and drivers must walk around their vehicle to check for hazards and operators, drivers and workers on foot should be aware of blind areas.
Vehicle pathways is another consideration. As part of that, workers on foot should be located as far as possible from vehicle paths. Parking, toilet, and break areas should be staged away from the principal conflict points and in some situations, the route may be marked with temporary traffic control devices.
Serious consideration should be taken to marking pathways when deliveries of materials are completed by a variety of subcontractors and independent drivers unfamiliar with the site and procedures.
The same is the case when multiple operations occur near each other and when workers on foot are in the vicinity.
If employees are in the backing zone or it is reasonable to expect that an employee will enter the backing zone, the truck should back up only when an observer signals that it is safe to back, or a video camera provides the driver a full view.
Back-up alarms audible over the noise level also are indicated and supported by a ground guide signaling that it is safe to do so. Back-up alarm malfunctions that cannot be immediately fixed must use ground guide signals instead, or the vehicle should be taken out of service until the alarm is repaired.
Access and egress from highway construction and maintenance zones also present a challenge and can be addressed in the TTC and ITCP. The plans should include detailed protocols regarding how contractors will safely move personnel, materials, and equipment into and out of the work area with minimum disruption to traffic and exposure of workers to the traveling public.
The use of technology such as back-up alarms, cameras, radars, ultrasonic sensors, and radio frequency identification (RFID) systems also contribute significantly to safety.
Options abound in sourcing such equipment. Companies such as Brigade Electronics provides technology that augments the human eye in spotting safety hazards such as 360° camera systems, camera monitor systems, White Sound back-up alarms, obstacle detection sensors, obstacle detection radar and digital recorders, which help reduce collision risks and protect vulnerable road users by minimizing vehicle blind-spots and assisting drivers to maneuver safely.
The company indicates 70 percent of incidents happen during initial machine start-up and low speed movement because of poor visibility, and that blind spots can be on the front, rear, side and nearside of a cab.
Not only do blind spots limit visibility of those working around and operating construction site vehicles, but site workers may also be wearing ear defenders, restricting their ability to hear approaching machines, according to Brigade Electronics.
Reading Truck offers tips on how to improve work truck safety.
It starts with having a plan that is conveyed to everyone. The first step is preparing drivers to join the fleet with best management practices through an online training course that can include videos, tests and interactive programs.
Management should run a motor vehicle record check on potential drivers to check for DUI/DWI convictions or a record showing poor driving habits – something that should be repeated periodically to ensure a driver still maintains safe habits. There should be no tolerance for speeding or impaired driving.
Behind-the-wheel training comes next, which is especially useful for those new to driving service trucks.
Consistent newsletters and emails highlighting safety messages – including any policy updates – help keep safety uppermost in drivers’ minds. Include situational information, such as best practices for driving in certain weather conditions, such as on ice. Focus messaging on topics relating to a batch of similar accidents so drivers are aware of not repeating the mistakes.
Reward good driving with recognition, such as a cash reward to drivers who are accident-free over a period of time or paid time off.
Reading Truck echoes the field safety messages promoted by other companies and government regulatory agencies: daily vehicle inspections, designating a spotter, directing traffic away from workers, reducing distractions such as the use of personal cell phones, and including signage at the worksite.
Ensuring work truck equipment is secure is another must, preventing loose material from flying off and causing damage or harm.
With more than 70,000 accidents occurring each year due to drivers falling asleep at the wheel, drivers who appear to need sleep should not be allowed to operate a work truck. Seatbelt use should be mandatory for the driver and passengers; drivers should never try to fit more people in their work truck than there are seatbelts for passengers to wear.
Truck ergonomics play a key role in driver safety. Some improvements include the use of a recessed frame-mounted bumper with LED marker lights for increased safety. As crew members use the bumper to step on and off the back of the truck, a sturdy and anti-slip surface is essential.
A Redi-Safe non-skid application prevents surfaces from getting slick after they have become wet or soiled. The material is not ignitable, making it suitable for welding applications.
External lighting on a truck provides additional safety for those who must work at night or early in the morning, helping workers use equipment safely in low-lit or dark situations.
Access ladders and steps enable workers to safely enter and exit a truck bed, especially if it is high off the ground.
Rear access doors are sometimes kept open while driving to fit in larger materials in the vehicle. They should be designed to not cover taillights so other drivers will be able to detect when the truck is braking or taking a turn.
With all these considerations in mind, put together a detailed and vigilant plan to keep workers and civilians safe from unintentional contact with equipment or objects on construction jobsites. Review the plan quarterly or as needed to ensure continued safety compliance. Most of all, stay safe out there.