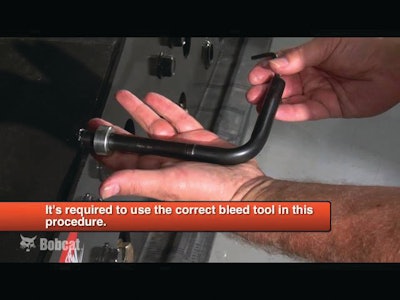
Keeping the rubber tracks on compact track loaders (CTLs) and other machines clean, maintaining their tension and inspecting them regularly can cut your operating costs significantly. Here are some things you need to know.
You CAN reduce wear
Wear and tear on guide/drive lugs due to side wear and debris ingestion can lead to rubber coming off in chunks and eventual tear-off. Carcass damage also exposes internal cables to damage, which makes them unserviceable.
- Use three-point turns: As often as possible, use three-point turn-arounds to reduce side wear; particularly when on pavement or very hard surfaces. A CTL will make zero-radius turns like a skid steer, but track is a much more costly than tires, and more sensitive to side loads.
- Don’t work in cutting environments: Working in sharp rock, steel and other cutting debris can be a misapplication of CTLs, unless your machine is riding on steel tracks.
- Keep tracks clean: Compact track loaders should be pressure washed at the end of every day to reduce track friction with debris and to allow checking for excessive wear such as flat spotting.
- Repair problems immediately: Find and fix the source of oil leakage from rollers, hoses or travel motors without delay. None will get better with time.
"The end of the day wash-down process is a good time to remove embedded foreign objects from the tracks and lubricate all moving parts," says Cameron Stejskal, product specialist, Terex Construction Americas. “The daily wash down is also an excellent time to look for any loose, worn, cracked, bent or missing components."
Tensioning: track life vs. convenience
Commit the effort to keeping track tension properly adjusted.
- Check tension every 50 to 100 hours according to the manufacturer’s recommended procedures of use. Adjust the frequency of your tension checks based on the success of the process. If every time you check them, the tracks are way out of adjustment, you need to shorten the interval.
- Over-tensioning will cause premature wear; even early failures in some instances. It also uses more power and fuel.
- Under-tensioning can allow the loader to walk out of the track, putting your operator in a potentially dangerous situation and possibly damaging the track or the machine.
"If you want to run to one side or the other within the specification (range), our recommendation would be to run them slightly on the loose side, because running on the tight side really doesn't do much for you," says Mike Fitzgerald, Bobcat loader product specialist. "If they are loose, the material will shed better. However, if they are way too loose, the tracks will come off; you can go too far."
Track replacements: get what you pay for
"Improper tension, improper operation and/or derailment can all cause damage to the rubber carcass and the internal structure of the track," says Kevin Coleman, Caterpillar skid steer and compact track loader product manager. "Once the track can no longer maintain proper tension and/or efficiently transfer power to the ground, it may be time for a replacement.”
CTL track is a highly engineered product that has to match the sprockets, rollers and idlers on your machine if you want maximum return on your investment.
"It is critical to have the right length and pitch of track so it matches properly with the sprockets," says Bobcat’s Fitzgerald. "If it doesn't match you will prematurely wear either the metal imbeds, the sprocket on the machine, or both. You may run into problems with either cables in the track or imbeds breaking prematurely."
But the right fit is no guarantee of track life.
"Manufacturing processes and rubber compounds have a huge effect on the quality of the track being purchased," says Cat’s Coleman. “OEM parts have been designed and tested to work with your machine to produce maximum machine productivity and maximum track life. Aftermarket tracks may cost less, but the life you achieve will likely be proportional to the cost."
As if to illustrate the variability in track quality, Bobcat offers two different types of rubber tracks for its loaders.
"We have the OEM track that we send out of the factory," says Fitzgerald. "Through our parts operation we also offer a less-expensive alternative track, which meets original design specifications, but will not have the same life due to differences in the rubber content or compound. It is lower cost, but it is not going to last as long."
More on maintaining CTL tracks:
Common Failure Points for Rubber Track