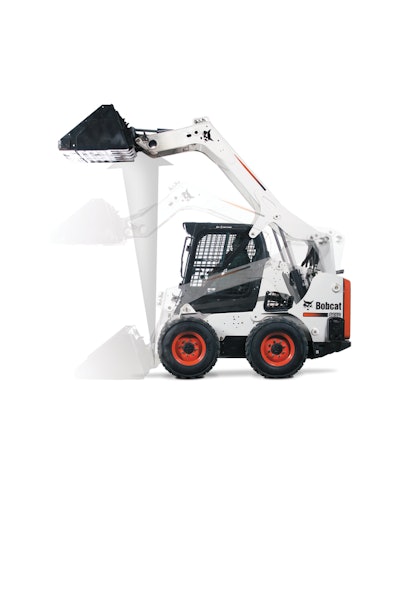
Before recommending skid-steer loaders to your customers, it’s useful to have a firm understanding of how loader boom arm geometry affects machine performance.
Two basic boom geometries exist – radial lift and vertical lift. The key differences in the loader arm lift path are due to the design of the loader linkage. A radial machine typically features a single pivot for the loader arms while the vertical lift model uses a more complex linkage which provides the vertical lift motion.
Differences in the machines are rather subtle. Performance is virtually identical when the loader arms are not raised and either machine is capable of accomplishing the assigned task.
Two primary advantages of a vertical lift machine are that it keeps the load closer to the machine through much of the lift cycle and it offers a greater overall lift height. There are many different vertical lift designs, so consult the lift patch chart for the particular make or model you are considering for specifics.
Vertical lift does not mean the load travels straight up. “Vertical lift is a bit of a misnomer because everybody is moving around a couple of different linkages,” says Tony Sims, segment development manager, Volvo Construction Equipment. “It usually follows some sort of S curve. But that curve is overall much closer to the center of gravity of the machine. All of the lift paths are just slightly different between different manufacturers.”
The difference in lift height between a vertical lift and radial lift machine is significant. “There is about a 30% difference in reach at full lift height between vertical and radial lift machines,” says Greg Rostberg, Bobcat marketing manager. “Because you achieve maximum reach in vertical lift machines at full lift height, it’s easier to clear high-sided truck boxes and hoppers. A vertical lift machine is also better for placing heavy pallets of block or sod.”
But you need to look at more than just the overall height. “You also need to look at height to hinge pin as this affects reach,” says John Comrie, Volvo Construction Equipment. “It is a good idea to always check the specs.”
Vertical lift machines may also offer advantages when working in confined areas. “With the vertical design, the bucket raises in a uniform straight line, so your overall dimensions remain the same while lifting and turning at the same time,” notes Tim O’Brien, brand marketing manager, Case Construction Equipment. “This is the reason vertical lift is preferred for loading dump trucks – the operator only has to position the machine once when approaching the truck and gets maximum reach at full height to load into the center of the truck body.”
The maximum height of the vertical lift machine gives it a large advantage when loading dump trucks. It allows a bucket to reach completely inside a truck to dump the load. “The operator may not be able to fully dump the bucket on a radial lift machine,” says Sims. “On the radial lift, the load is much closer to the cab, which can allow material to fall back on the loader.”
Bobcat Company explains its radius lift path design provides greater forward reach than a vertical lift path for more than 80% of the lift arm path, including a greater maximum reach at mid-range heights. “Since the arm is moving in an arc, a radius path has more reach through most of its path than a vertical lift path system,” notes Rostberg. “Radial lift path machines provide maximum reach at truck bed height, therefore this type of machine excels in jobs at mid-range heights like dumping over a wall, backfilling or unloading flatbed trucks.”
Consider reach
Radial lift machines provide the greatest reach when the boom arms are parallel with the ground. “This is typically eye level,” says Sims. “This is beneficial when taking loads off flat bed trucks. If you have pallets stacked side-by-side on a truck, it is sometimes possible to reach the second deep pallet from one side of the truck.” It is also beneficial for spreading material where you want to get close to a curb or a ditch with your bucket at mid height. “You have more reach capability across the obstacle with the boom at mid height.”
The differences in the arc travelled by the loader arm create unique reach characteristics. “A radial machine, at mid-lift, will provide a bit more reach in front of the machine than with a vertical unit,” says O’Brien,”while a vertical unit provides a constant reach all the way through the lift cycle.”
Vertical machines can be rated for slightly higher operating capacity because they keep the load closer to the center of gravity. “This offers greater stability,” says O’Brien. “Hydraulic lifting capacity of a radial is greatest at or near ground level vs. the vertical design, which starts with lower lifting capacity at ground level but increases through the lift cycle.”
The farther the load is from the center of gravity, the less stable the machine. “Radial lifts really push the load out further at mid height, and that is the most unstable point for those machines. Keeping the load closer to the center of gravity of the vertical lift machine also improves the overall stability.”
Consider the example of a Volvo radial lift skid steer versus a Volvo vertical lift loader. “The tipping load for the vertical lift MC115C is 5,448 lbs.” The radial lift MC110C offers a 4,908-lb. tipping load. That is a difference of 540 lbs.
Excavation performance
Radial lift machines are best suited for digging and excavation applications. There are typically only two pins to attach the loader arm to the machine with a radial lift design. This means fewer pivot points to maintain and possibly less side to side movement.
“Both machines can dig very well,” notes Sims. “The key difference is the number of maintenance and wear points. Vertical lift systems have many more lubrication points and pins. Digging fresh dirt is certainly a very tough job and the less that can go wrong the better. Another application is recycling. This is probably the toughest application for these machines. I certainly encourage customers to go with radial lifts in those situations.”
O’Brien agrees, “Radial machines are better for rough or heavy-duty applications, including breaking, prying or hard digging. The Case Alpha radial lift arm design contacts the frame while digging for greater leverage and durability because the dynamic forces project horizontally rearward through the mainframe.”
The breakout forces are very similar between radial lift and vertical lift loaders. “But the perception is that a vertical path machine has a higher breakout force because it lifts straight up and takes the material with it without moving the machine,” notes Rostberg. “With a radial path machine, the machine has to dig into a pile and then back up to lift and move the material. Regardless, breakout force differences are negligible.”
There may be a misconception that bucket breakout force is related to the boom lift system. “Bucket breakout force is really independent of the boom lift systems,” says Sims. “It just has to do with boom geometry, how the bucket cylinders are orientated, what kind of pressure those cylinder can put out and how they are aligned with the bucket.”
The choice between radial lift or vertical lift systems really boils down to your application. “Any sort of landscaping, material handling, pallet fork work and load and carry applications are all strong candidates for vertical lift machines,” says Sims. “Individual operators really appreciate the increased lift capacity and comfort when carrying a load.”
Most manufacturers only offer radial lift on the smaller size machines. “The vast majority of loaders with operating capacities greater than 2,000 lbs. are vertical lift systems,” says Sims. “They want that lifting capacity on those larger machines.”