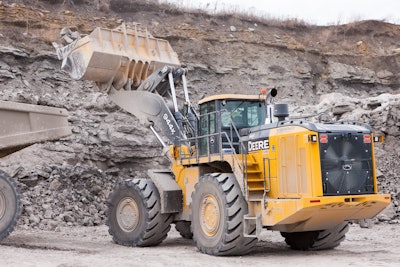
Electrification is a predominant trend in the construction equipment industry. The corresponding introduction of software allows machines to gain efficiency.
“With electrification, we can do more with the software,” says Scott Young, director of electromobility, Volvo Construction Equipment. “We can tailor for the customers’ application, site or environment so the machine is purpose built for what they are doing. We are starting to see electrification of subsystems in the machines starting to come onto the market.” This allows decoupling of systems, so that systems such as the hydraulics will not be dependent on engine speed.
Future use cases of electrified machines will depend on the application. “We see segments where you have fully electric machines, machines connected to the grid and hybrid machines,” Young comments.
Hybrids offer many opportunities. “As we hybridize, we can downsize engines and recuperate energy, leading to fuel savings and reduced emissions,” Young points out.
Hybrid technology currently entering the market is predominately diesel/electric. “Technically, the word hybrid means two sources of energy,” says John Chesterman, product marketing manager - production class four-wheel-drive loaders, John Deere. “The key is we can recover energy.”
Drivers Behind Adoption
Research on hybrid construction equipment began in the late 1990s and became commercially available in 2003 when Hitachi launched a wheel loader that utilized a series hybrid powertrain. Since then, many OEMs have launched various hybrid technologies that range from series and parallel diesel/electric hybrids to plug-in hybrids and hydraulic hybrids, and even flywheels.
To date, the adoption rate in the U.S. has been fairly slow. It is very dependent upon segment, application and the legislation and regulation. It is advancing more rapidly in Europe and in other parts of the world because certain cities are targeting low-emissions zones or setting future goals of zero emissions.
“As the costs come down, we will see it become more mainstream,” predicts Jessica Shetler, product marketing manager, construction and forestry engine and drivetrains, Deere & Company. “Contractors are seeing the benefits in the machines available today. Having the customer’s return on investment be a value is the main driver right now. It comes down to the cost of the components and what you can get for productivity.”
Hybrid technology is used throughout the automotive industry in many different forms. “It is a great indicator for what heavy machinery will be doing,” says Shetler. “The automotive industry is going to help drive cost down, as well as drive confidence in that technology.”
The size of the machine will have a definite impact on whether hybrid technology is beneficial. “For example, on a machine that burns 2 or 3 gal. an hour and is run 1,500 hours a year on an average basis, fuel is usually a small part of the cost of the machine,” notes Chesterman. “The benefit on ease of operation and productivity tends to be a much bigger driver.”
On larger machines, such as the John Deere 944, the ROI equation changes, especially since contractors are often replacing older generation units that are far less efficient, burning a fleet average around 9 gal./hour. “Applications have a great effect, but customers are seeing big, significant decreases [with the 944 Hybrid],” says Chesterman.
But fuel savings can’t come at the expense of performance. “At the end of the day, most owners... don’t want to sacrifice productivity for fuel savings,” says Justin Lantin, product marketing manager, Komatsu excavators. “As far as Komatsu, the hybrid systems have evolved into more performance oriented while still maintaining the fuel savings. To improve production, we have remapped our software so you will get more performance while still maintaining significant fuel savings... We can get faster cycle times, quicker spots out of the machine.”
Wheel Loader Operation is Simplified
To date, wheel loaders and excavators have proven well suited to hybrid technology. Wheel loaders are subject to frequent starts and stops during typical V-cycle loading. In a conventional machine, a lot of energy is wasted through braking.
Hybrid systems for these machines typically include series, parallel and series-parallel hybrids. A series hybrid system is the most simplistic. The engine powers a generator and the hydraulic circuit. In turn, the generator powers electric drive motors. In this system, the engine is mechanically decoupled from the drive wheel drive motors. This allows the engine to constantly run in its most efficient speed and torque range.
A parallel hybrid powertrain uses two separate power sources that can directly power the drivetrain. The engine can directly power the wheels and is mechanically coupled to the wheels so there is less energy lost when converting from mechanical to electrical energy and back again.
With the series-parallel hybrid wheel loader, the parallel separate power sources can directly power the drivetrain while the hydraulic system is driven in series, decoupled from the engine. This allows the hydraulic system to work independently from the engine.
Whenever the electric motor in the 944 Hybrid is being driven by the momentum of the machine, i.e. coasting down a hill or in the middle of a V-pattern, it is recovering energy from the electric motor and sending it back through the system.
“Each generator powers one front wheel and the opposite rear wheel,” Chesterman explains. The primary implement pumps for the boom and bucket are also on that gearbox. “Whenever an electric wheel motor is being driven by the momentum of the machine — i.e., coasting down a hill or in the middle of a V-pattern — we are recovering energy from the electric motor and sending it back through the system and using the generator as a motor to turn the gearbox. The power can go in both directions.”
This results in significant fuel savings. “In almost any diesel engine, whenever the engine is being driven, generally its fuel state goes to zero,” says Chesterman. “We have had long load and carry applications where one portion of it was downhill. If the operator wants to coast down the hill, the engine will show a zero instantaneous fueling rate. If we use the electric motors to recapture energy, we can keep the engine at zero state as long as possible.”
On the performance side, electric wheel motors greatly simplify bucket loading for the operator compared to a torque converter machine. This makes it easier for novice operators.
“In a normal wheel loader with a powershift torque converter, the operator is really controlling engine speed with the accelerator pedal,” says Chesterman. “You also control the pushing power because pushing power is related to how the torque converter is multiplying the torque. The operator has to be able to coordinate between how the hydraulic speed might change; because if I change engine speed, I change hydraulic pump flow and how I want the loader to push into the pile.”
The hybrid eliminates this balancing act of engine speed vs. pushing power vs. hydraulic response. “With the hybrid machine, that pushing power has nothing to do with engine speed,” says Chesterman. “Generally, when an operator commands the hydraulic flow on a hybrid, the boom is going to go where you want, and when you step on the accelerator, it is how hard you want to push into that pile. It makes it very easy for unskilled workers who don’t have the coordination down.”
“That right now is the biggest benefit in the industry,” says Shetler. With the operator shortage, it’s a major advantage to have an operation where you can hire just about anyone off the street who knows how to drive a car and have them hop in a loader and be productive quickly
Volvo recently completed a test of its prototype LX01 Hybrid Wheel Loader with Waste Management in California where it achieved a fuel savings averaging 45 percent.
[VIDEO] Operators Share Experiences with Volvo LX1 Prototype Hybrid Wheel Loader
The use of a much smaller engine in the LX01 than typically found in this size of machine enables the loader to have a steeply sloped rear hood. “It allows the operator to see an employee on the ground much closer,” reports John Meese, senior director of heavy equipment for Waste Management. In addition, the use of four electric wheel motors prevents damage from debris. “When you look at the way the machine is built, there are no axles underneath it because the machine has four electric motors inside the wheels. The whole bottom side of the LX is clean.”
The decreased noise levels due to the hybrid power system and adjustability of power output were also benefits. “There is immediate power,” Meese states. Wheel spin could be controlled through a laptop computer. Likewise, boom and bucket tilt speeds could easily be tailored to operator preferences.
“These are functions you cannot do with a typical, conventional wheel loader,” says Meese.
Electric hybrids often bring benefits in terms of software-driven features not available on conventional machines. One example is the traction control system on the 944K Hybrid. “No other wheel loader in this size class offers traction control. With four tires costing around $60,000, this offers a significant competitive advantage,” Chesterman states.
Four independent electric wheel motors make the traction control possible. Most conventional machines in this size category use an open front differential that can cause operators to spin the tires if they don’t carefully modulate the throttle or the impeller clutch torque converter during the loading process.
Quicker Excavator Response
Excavators require a different approach to hybrid technology due to the nature of their operation. Two main areas where hybrid systems can capture wasted energy — and thus increase performance and efficiency — are the braking kinetic energy of the swing drive and the gravitational force on the boom.
Like loaders, excavators can use series, parallel or series-parallel hybrid technology. With the series architecture, the engine directly drives a generator, which is then used to power the swing motor and motors to power the hydraulic pumps.
The Komatsu 365HB LC-3 hybrid excavator uses an electric swing motor and hydraulic pump motor assist to provide quick response for increased productivity.
When the swing of the machine decelerates, the electric swing motor charges the capacitor. “It is a very similar principle to regenerative braking on a car,” says Lantin. “Once you let off the swing, that electric motor is kicking back electricity to the capacitors. Now you have stored energy.”
In addition, the generator motor between the engine and hydraulic pump acts like an alternator, charging up the capacitor for when the energy is needed. The capacitor can help power the electric swing motor and hydraulic pump motor to help supplement the engine horsepower.
“You are not using as much horsepower as you typically would,” says Lantin. “You are providing electricity to the swing and electric assist to your hydraulic pump. Not only does that save fuel because you are not working your engine as hard, but more significant is the response. Electric power is instantaneous, so when your hydraulic pump demands a lot of power, that electric motor will implement instantaneous torque. You get a very quick response to your hydraulics.”
Since electric components are controlled by software, it is possible to tailor machines for preferences. “We are able to adjust the response rate or sensitivity of that swing function,” says Lantin. “Your swing acceleration and swing deceleration is fixed on a hydraulic excavator.”
You can also fine tune the assist to the hydraulic pumps. “You can adjust the ratio if you want to put a little more to the swing acceleration or into the pumps,” says Lantin. “When you put a little more assistance to the pumps, you tend to see faster boom up speeds.”
The HB365 LC-3 is the latest hybrid in Komatsu’s lineup, and it has a conventional equivalent, the PC360 LC-11. “Structurally, they are pretty much identical,” says Lantin. “I would say... we are at about 80% identical part for part. The 20% are those big components — the swing motor, the capacitor.”
Komatsu advertises up to a 20% decrease in fuel consumption for the hybrid, but it also comes with a price premium. “As for ROI, it really depends on utilization,” says Lantin. The excavator earns a maximum ROI in high-production applications that utilize a lot of swing, such as scrap handling or crusher loading. “The higher the utilization, the higher the savings.”
That is one reason hybrid technology currently makes more sense on larger excavators. A 30- or 40-ton machine typically runs an average of about six hours a day, according to Komtrax telematics data. “You move down into the smaller machines and you start getting three to four hours a day. [For excavators], the 20- to 30-ton class has been the stepping stone for most of the OEMs,” Lantin indicates.
“As you go to smaller machines, it is a question of do you hybridize or do you go directly to electric,” Young adds. “Your power demands, applications and use requirements are different with some of the higher productivity machines.”
Building Confidence in Production Machines
Hybrid technology makes sense on 50-ton and larger excavators, but currently no one is offering the technology in this space. “You will see a higher fuel savings because those tend to be mass production machines,” says Lantin.
To address concerns about component longevity, Komatsu offers a five year, 7,000-hour hybrid powertrain warranty. “It gives the customer peace of mind, especially since they are not used to how long the components last, the durability of the components. There is a lot less wear and tear on the engine now and also on the hydraulics,” Lantin states. “You are basically taking a lot of work out of the hydraulic system and the engine and supplementing it with another system. So theoretically, you can expect longer life out of these components.”
Similarly, John Deere offers an eight-year, 20,000-hour electrical assurance warranty on the electric motors, generators and power electronics on its 944K Hybrid. Yet, not everyone is concerned about the durability of electric components.
“I have customers who have worked in big mines,” says Chesterman. “They are very accustomed to electric power in draglines, big shovels, even in some haul trucks. Most quarry operators also use a lot of electricity. They either have mobile generation or they are on the grid. All of their crushers, stackers and conveyors are electric.”
These operators have less apprehension about electric components, and may even prefer electrical-proven powertrain components.