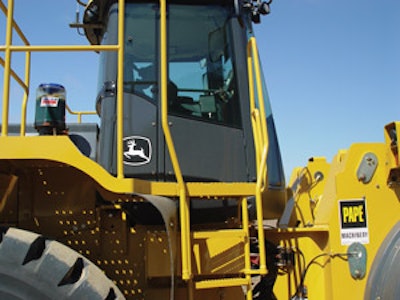
Longer component life is the main reason to invest in an automatic lubrication system. "The owner is assured that all components are being lubricated," says Drew Cherven, manager, national accounts, Lincoln Industrial. "Daily grease lubrication can, at times, be overlooked when relying on manual point-by-point lubrication with a grease gun or even a lube truck."
With autolube systems, lubricant constantly flows to the bearings. "The machine is lubricated dynamically, while in motion, overcoming loads and allowing grease to protect all wear surfaces," says Cherven. "And that lubrication is applied in small, proportioned amounts, often every hour, replenishing used grease and purging contaminants."
Another benefit is reduced maintenance - both scheduled and unscheduled. "You don't need to spend that time greasing," says Dan Mathews, worldwide product marketing manager - mobile, Graco Inc. "And if you can prevent failures in the first place, you save time and money on unplanned maintenance."
Consider the time it takes to properly grease a piece of equipment every day. "An automatic lubrication system allows 30 to 45 minutes a day of increased productivity," says Cherven.
Normal operations, such as switching buckets, can also be simplified with the use of an autolube system. Since the coupling has been lubricated more frequently, the bucket pins are more easily removed, Mathews points out. Any greased components that need to be replaced are more easily removed, improving repair efficiency.
"An additional important benefit is safety," says Scott Davies, district manager, Lincoln Industrial. "Anytime you can avoid having someone crawling around on top of and below machinery, it is a significant benefit."
The cost equation
When determining whether equipment can benefit from automatic lubrication, calculate the costs of potential downtime, repairs and labor associated with manual lubrication practices. Balance these costs against the up-front investment in the autolube system to find your break-even point.
The cost of an autolube system depends on any custom needs, the number of lube points and the pump size. "It varies greatly from $3,000 to $7,000, depending upon the customer's equipment lube requirements," says Mathews.
The simplest manual systems bring connections from all of the lubrication points back to a single block. "Then you hook up a grease gun to that single block and pump it manually," says Mathews.
Most fully automatic systems are used on larger production machines. "Ninety percent of the applications are for excavators, wheel loaders and haul trucks," says Davies. "The costs can range anywhere from $6,000 to $8,500, depending on the machine type and the alarm system options chosen."
Line protection and routing issues heavily influence installation costs. "Excavators are the most expensive, because they require the most guarding and relocating of some of the lube points to protect feed lines in ground engagement areas," says Davies. "We relocate some points because, while the locations of the fittings on the bucket are convenient for manual lubrication, they are often in the worst place for installing a permanent feed line.
"Wheel loaders are the next most expensive, primarily because of guarding issues," he adds. "Haul trucks are the least expensive because they require minimal line protection (spiral wrap)."
The pump is the highest priced component on an autolube system. But the more lubrication points a piece of equipment has, the more this cost is dispersed. "The cost per point for a fully automatic system decreases as the number of points increase," says Mathews. "You are just spreading that fixed cost over a variable amount of points."
Call in the experts
Because of their complexity, installation expertise is definitely required. Graco distributors FD Johnson and Howard Marten have vast experience installing these systems on construction equipment. "We basically supply the components to them and they install them on the fleet of equipment," says Mathews. This experience is critical.
When a system is designed, you need to determine how much grease each point will receive. "Based on their experience and knowledge of these machines, FD Johnson and Howard Marten have their designs already set," Mathews notes. "They have watched these machines operate for years."
Davies also emphasizes the need for specialized expertise. "It has been our experience that these systems need to be designed for each machine by someone who is well trained and has significant experience," he stresses. "This is not a job for the contractor. The variation of the needs of each point on any given machine can fluctuate so much from one manufacturer to the other that it makes end-user installation inadvisable."
Installation time varies widely by equipment type. "Excavators take about 20 man hours, give or take a few hours. Wheel loaders may require 12 to 16 man hours and haul trucks need about 10 to 16 man hours," says Davies. "These times vary because not all machines are the same. For instance, one manufacturer's haul truck can have many more points."
FD Johnson and Howard Marten estimate it could take up to 20 to 35 man hours. "It varies according to the number of lube points, the difficulty of removing existing grease fittings and fitting lines, and the ability of a joint to accept lubricant," says Mathews. "You might fire up your system and find out one of your fittings is clogged, so you have to go in and fix that. The customer's preferences for protecting the lube lines also factor into the increase or decrease of installation time."
Understand the ROI
Although the overall investment in time and cost is fairly substantial, the ROI from automatic lubrication can be rather quick. "Our main customer says his return on investment is usually less than a year," says Davies.
"We have found that 95% of the costs related to manual lubrication can be eliminated by using an automatic lubrication system," Cherven asserts. "Five percent is still required to inspect the system and refill the reservoir."
In addition, he cites, "Research shows that 50% of component failures can be eliminated by utilizing automatic lubrication systems. The other 50%, if incurred, are caused by extreme environmental conditions, misalignment and other factors not related to lubrication."
"As a rule, once [contractors] try their first system and realize the benefits first hand," says Don Fithian, national account manager, Lincoln Industrial, "they want to begin a program to retrofit their other machines and not revert back to the manual lubrication method."
Maintenance Still Required "A reservoir that does not require refilling is a definite sign of a problem," he continues. "It is not a bad idea to log grease consumption like you would oil consumption." Some contractors don't use autolube systems because they feel this gives the technician the opportunity to inspect the machine while greasing. Yet, inspections should still be done when a system is installed. "We recommend a quick, daily walkaround inspection of the system, ensuring all lines and fittings are connected and have not been hit or impacted by the environment," says Drew Cherven, Lincoln Industrial. "We also have a manual push button on our pumps to instigate one cycle of the system. This allows the operator or mechanic to observe the performance." |
Mustang Rental Service Reduces Failures "It just doesn't happen," says Bill Anderson, Mustang Rental Service. "Customers just want a piece of equipment that is going to work. If one breaks down, they expect you to bring another one if you cannot fix it in a reasonable amount of time." A lack of periodic greasing used to cause expensive downtime with the company's articulated dump truck fleet. "We had issues with the cylinders that raise the dump bed," says Anderson. Without proper greasing, the bearings that were holding the cylinders were wearing out very quickly. "It was causing them to get in a bind and actually scar the inside of the cylinders. That metal was traveling throughout the hydraulic system - it would completely trash the system. A typical failure like this was in excess of $30,000." The autolube systems have cured the problem at a cost in the neighborhood of $3,200, including installation. The installation was done in house. "I have a guy who can do it in about eight hours," says Anderson. All pivot points are now serviced by the lubrication system. The systems have proven reliable. "The failures, more than anything, have been operators messing with stuff that they really shouldn't be messing with, causing breakers to trip and things like that," says Anderson. Maintenance is performed every time the trucks return to the rental house. "When they come in off rental, we will refill them with grease and test them," says Anderson. "It is easy to make sure they are working just by the nature of how they work. On the blocks that distribute the grease, you just look for the plungers and make sure they are moving. If those plungers are moving, you have grease moving throughout the system." On rare occasions, hoses that supply the grease can get pulled off due to the routing of the lines. "It has been trial and error," says Anderson. "When we have that happen, we analyze what happened and figure out a way to prevent it. We have a pretty good installation system now. If it does get ripped loose, there is a good reason for it." In addition to the articulated trucks, the autolube systems work well on demolition hammers. "With a hammer, you are looking to grease the upper and lower bushings that the moil point rides in," says Anderson. These points typically require greasing every two to four hours. "So we have systems that will grease continuously. If the hammer is running, it is being greased." This has increased hammer life. "You are keeping a layer of lubricant in there," says Anderson. "If you have a good seal, you are preventing dust from the concrete or whatever you are breaking from getting in there." For Mustang Rental Service, the autolube systems have solved lubricant-related failures. "Anybody who is having problems like that, I would encourage them to take a serious look at lubrication systems because they will definitely pay for themselves," says Anderson. |