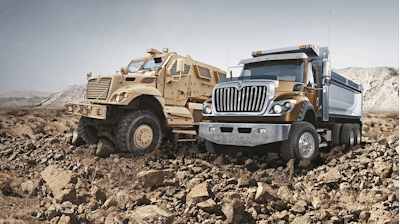
Gaining access to remote, muddy or sandy jobsites can be a challenge. Differential locks, Central Tire Inflation Systems (CTIS) and all-wheel drive provide solutions, but each technology comes with limitations and drawbacks.
CTIS works by lowering the tire pressures, which results in a larger tire contact patch on the ground and therefore increased traction and flotation. “Some customers, [mostly working] in sandy soil, swear by CTIS,” says Dave Hillman, vice president of vocational marketing, Navistar. “Those systems, when coupled with rear differential locks, tend to be very functional.”
But CTIS requires the driver to be proactive. “You have to know that where you need to go may require a wider contact patch, so you deflate the tires preparing for that,” notes Hillman. He adds that interest in CTIS systems tends to fluctuate. “CTIS comes around every once and a while and then fades away. I don’t hear a lot of customers asking for it. But it is another technology some customers have explored in lieu of a front driving axle.”
Front-driven Axles Expand Access
All-wheel drive (AWD) lets you traverse terrain that would otherwise stop trucks in their tracks. “There are various conditions where either a 6x6 or 8x8 will thrive, including mud, snow, ice or even above-normal grades,” says Dan Souhan, sales and marketing director, Marmon-Herrington. The company has provided powered axles since 1931.
“A 6x6 and/or 8x8 can have a significant impact when it comes to off-road gradeability due to the additional tractive effort it provides,” says Souhan. “Any time you can add an additional driving axle or two, you’re going to see a significant increase in performance because more axles/tires are providing tractive effort. This is most noticeable in severe on- and off-road conditions where wheel slip is a common occurrence. The primary consideration is the amount of torque that is required for providing optimal performance. A mechanical system is going to provide the maximum amount of torque without the worry of a hydraulic line bursting or the reduced torque level of other systems in the market.”
Like any technology, there have been numerous improvements in the installation and/or performance of 6x6s and 8x8s. “Some of these changes for the axles and transfer cases as it pertains to performance would include high-efficiency bearings and improved lubes for increased efficiency,” says Souhan. “Marmon-Herrington’s double reduction planetary axle design also allows the use of double cardan joints for enhanced maneuverability. Another improvement would be air disc brakes for improved stopping. [The company] will launch disc brake offerings in 2018.”
Aluminum housings also provide significant performance benefits, from reducing chassis weight to reduced heat generation. “We’ve also recently launched a new Safe Shift All-Wheel-Drive Protection System for eliminating transfer case shift-on-the-fly failures,” says Souhan. “This new system is something that Marmon-Herrington includes with all in-house conversions.”
As with any technology, front drive axles also come with a few potential drawbacks, including increased weight, cost, complexity and in some cases a higher center of gravity. “The height, cost and weight tend to be the top three issues; and depending upon the customer, the order changes,” says Hillman. “With some customers, height is more important, with others it is weight and with others it is cost.”
There is often a slight trade-off in fuel efficiency, as well. “Front drive steer axle manufacturers realize this and try to minimize it as much as possible,” says Souhan. “Some of the methods used for achieving this include the use of high-efficiency bearings, improved lubes and other proprietary methods. There are also other designs available that provide AWD capability without the loss of fuel efficiency, but they are severely limited in terms of speed and available torque.”
Due to the cost, AWD tends to be reserved for the most demanding applications. “While initial acquisition costs for an AWD option can be considerable, it can easily pay for itself by reducing the need for towing and costs associated with downtime when rear suspension-driven trucks get stuck,” says Samantha Parlier, vice president, Western Star Marketing and Product Strategy. “Western Star offers factory-installed AWD in a variety of models and configurations.”
Freightliner Trucks also offers a full line with AWD to meet the requirements of different applications. This ranges from the M2 4x4 for light applications up to the 114SD for severe duty with a set-back axle and drive axles rated at 20,000 and 23,000 lbs. “Typically, all-wheel drive improves off-road performance, but how much it improves performance depends on the setup,” says Kelly Gedert, director of product marketing for Freightliner Trucks and Detroit Components. “What’s important is that the customer works closely with the vocational salesperson to spec their truck. Freightliner dealers have a deep understanding of the best equipment needed based on application and terrain to ensure optimal performance.”
Understand Trade-offs
If you are in an application where you are getting paid to deliver a product, the weight trade-off really deserves close attention. “Everything that we do with a front driving axle has a transfer case aft of the transmission that splits the power,” Hillman points out. “So you have the weight of the transfer case. You have another driveshaft and then you have the delta between a non-driven front axle to the driven front axle. It’s probably over 2,000 lbs.”
Of course, weight depends on the configuration. “The amount of weight added to a 6x6 configuration is mostly dependent on the axle, transfer case and suspension selected,” says Souhan. “An estimate can vary greatly, and as an example can be anywhere from 1,200 to over 2,000 lbs., depending on the final configuration.”
Marmon-Herrington works to minimize this additional weight as much as possible by using lightweight double reduction planetary axles and aluminum vs. steel transfer cases. “For example, certain transfer cases that Marmon-Herrington offers can save upwards of 50% [of the] weight as compared to competitors,” says Souhan. “The double reduction planetary axle not only provides the customer with the most durable axle available, but also does it in a reduced weight package compared to single reduction axle designs. This allows our customers the opportunity to have the durability, dependability and torque of a mechanical system while minimizing the added weight.”
“The Western Star AWD option can be equipped with a single- or two-speed transfer case, which contributes to excellent gradeability and traction and is ideal for low- and high-speed operations,” says Parlier. “AWD trucks can be spec’d to perform just like on-highway trucks. The transfer case can be equipped with integral air shift controls for front axle engagement. There is added weight and loss of driveline efficiency associated with the AWD option, and while this can have an impact on fuel efficiency, customers need to evaluate their specific application and business needs. In general, customers who can benefit from the addition of AWD are not driven by fuel economy as their primary cost of doing business.”
There are also ways to offset the weight gains. “Lower displacement engines are typically preferred in AWD applications. They provide a lighter weight option to counter some of the additional weight added to the truck by other components, but still deliver the torque needed to optimize AWD performance when needed,” says Parlier.
Still, anyone who hauls payload must pay very careful attention to the weight penalty. “Customers who are paid to deliver a product, like for concrete placement as an example, need to be very specific on when they choose a front driving configuration vs. some other technology like differential locks to ensure their vehicles don’t get stuck,” says Hillman. In other applications where the truck performs a service, the payload weight may not be as important as gaining jobsite access.
There are tools that will help potential customers determine whether AWD is the best option for their application. “In our sales tools that we offer to our dealers, we have the ability to predict exact performance criteria — gradeability, startability,” says Hillman. There are many factors that influence performance characteristics including wheelbase, engine and gear ratio.
Mechanical drive front axle systems have improved over the years, as well. “One big [improvement] that we have seen working with some of our key suppliers has been the availability of offset bowls,” says Hillman.
Historically, the bowl has been in the center of the axle, which meant the trucks had to be lifted to gain clearance from the engine oil pan. “With the differential set off to one side, it allows us to have a lower chassis height than we have had historically,” says Hillman. But this does require a more complex driveline arrangement. “Instead of having everything aligned down the center of the chassis, you have shafts with a little bit of an angle to them.”
“Cab height has always been a challenge with 6x6 configurations and Marmon-Herrington is always reviewing opportunities to minimize cab height,” Souhan comments. “One example is the double reduction planetary axle that it offers. These axles provide a smaller bowl design for improved packaging and allow the chassis to sit lower on the axle. Another example would be [the company’s] step frame conversions. These conversions allow customers the benefit of maintaining factory body height.
“There are systems out there that allow the customer to maintain the cab height, but it’s the same system that offers significantly less torque (up to 60%), lower speeds (max speed 25 mph) and added hydraulic complexity,” he continues. “For extreme situations, the mechanical system still provides the optimum advantage in terms of torque and speed.”
Western Star typically sees its truck chassis raised by approximately 5 in. to accommodate its factory-installed AWD. “The increased vehicle ride height improves driver visibility and provides greater ground clearance, as well as improves performance navigating unimproved surfaces,” says Parlier, “ultimately increasing overall reliability and reducing costly downtime that can be caused by debris damage to the chassis and chassis-mounted components.”
Western Star does not see AWD as limiting the available performance. “Gear ratio selection is important,” says Parlier. “Front and rear axle ratios should match for AWD configurations and need to be compensated for if front and rear tire sizes differ.
“Ultimately, the specification of the truck is designed for the jobsite it will be servicing,” she adds. “Customers who select AWD do not have to compromise on performance, as there are a number of axle ratios available to meet the wide range of applications requiring AWD.”
Alternate AWD Technologies Emerge
Some of the newer AWD trucks don’t have a transfer case. Instead, the driveshaft to the front axle runs from the power divider on the front rear. When the power divider is locked, the front drive axle is also engaged. Eliminating the transfer case saves a lot of weight.
Terra Drive Systems has worked to overcome many of the challenges facing conventional AWD conversions, which include broken transfer cases and increased ride height. The company already had more than 40 years’ experience supplying hydraulic rear-wheel-drive systems for combines. Based on this experience, the company developed EZ Trac, a closed-loop hydraulic drive system designed specifically for the work truck industry.
The EZ Trac hydraulic AWD solution has been on the market for 10 years. Its benefits include its lower weight and its ability to maintain OEM ride height, retain the factory turning radius, enhance ease of use and reduce service costs. A cab-mounted switch engages and disengages the front axle on the go. No transfer case is required. It also maintains factory turning radius and is 800 to 1,000 lbs. lighter than traditional AWD systems.
A PTO mounted to the transmission drives a 6,000-psi hydrostatic pump, which is used to power the EZ Trac. The system can be retrofitted to most vehicles without putting extra stress on existing engine components. It is capable of delivering 110-hp output. Axles are available in 12,000- to 20,000-lb. weight ratings.
Navistar is also exploring a hydraulic option. “Through our partners with our Alliance, we are working with our European colleagues and the technologies that they have available that may be applicable to this marketplace,” says Hillman. “As an example, MAN has a hydraulically driven solution that they use for front axles. There are benefits that customers have implemented in other markets that may benefit customers in North America.”
Military Technology Meets Most Demanding Applications
Acela Truck Company has a mobility solution for the most extreme jobsites. It offers the Monterra 4x4 and 6x6 extreme-duty, high-mobility line of commercial trucks.
“These trucks were designed for the U.S. DOD to operate in the world’s worst conditions,” says David Ronsen, Acela founder and president. “The FMTV, which is the original truck platform that Acela builds on, is the only wheeled vehicle in the U.S. Army’s arsenal to achieve its ultra-reliability status.”
According to Ronsen, the vehicles can access places no other Class 7 or 8 truck (at least on-highway) can get to. “Our trucks are rated for a 60% slope at full GVWR and a 30% side slope at full GVWR,” he explains. “We boast a 14-in. under axle clearance, 23-in. under frame clearance, 47-in. tires and CTIS.”
CTIS allows tire pressure to be decreased at the press of a button down to 17 psi if conditions warrant. “That expands the tire’s footprint to such an extent that you almost turn it from a wheeled vehicle into a tracked vehicle,” says Ronsen.
The Acela Monterra fills a unique niche. “The ultimate problem that we solve is access. In North America, which is the only continent that does not have a production high-mobility, extreme-duty truck, we really bridge the gap between a heavy-duty truck and a tracked vehicle, or even an articulated vehicle,” says Ronsen. And it can typically access the most rugged terrain more cost effectively.
“Tracked vehicles have to be hauled in with another truck and trailer one at a time,” says Ronsen. “They cost a fortune to build, so the capital expenditure is huge, and they cost a fortune to maintain. Our 4x4 Monterra starts at $95,000 MSRP. With fleet discounts, that price drops pretty dramatically and pretty fast. A tracked vehicle may start at $225,000 to $250,000.”
The Monterras are also legal as on-highway trucks. “The engines met standards when they were built,” Ronsen points out. “We have two gearing options. One is standard military gears that top out at about 58 mph and offer exceptional low-end performance. The other is a high-speed option that gets you up to 74 mph.”
The frame rails are body-builder friendly with a standard 34-in. width. “I have seen just about anything you can imagine on the back of these truck chassis — snowplows, salt spreaders, snow blowers, service bodies, flat decks, cranes, fire bodies, booms,” Ronsen comments. If the body can fit on a Class 7 or 8 truck, it will fit on the Acela trucks.
A cabover design aides maneuverability. “Our turning radius is anywhere from 30% to 70% smaller than a traditional conventional cab truck,” says Ronsen. “The turning radius on our short wheelbase 6x6 is 56 ft. That is the equivalent of a medium wheelbase F-550. The cabover design allows you to have a much shorter wheelbase-to-payload area ratio. We still have the same amount of frame rail to work with, but our wheelbases are much shorter than a conventional truck.”