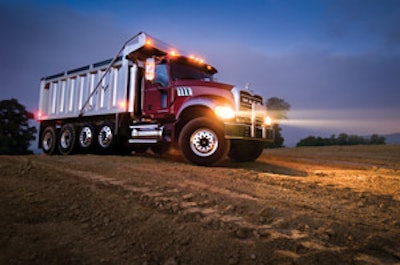
The Bridge Formula often drives the front axle configuration (axle forward or axle back) and the rear axle spacings of your vocational truck fleet. Congress enacted the Bridge Formula in 1975 to limit the weight-to-length ratio of a vehicle crossing a bridge. It establishes the maximum weight any set number of axles may carry on the Interstate highway system.
Under the Bridge Formula, the gross weight limits are determined by the length of the vehicle, the number of axles it has and how they are spaced. The formula is: W= 500 [(LN/N-1) + 12N + 36]
In this equation, W is the maximum weight (lbs.) that can be carried on a group of two or more axles to the nearest 500 lbs. L is the spacing in feet between the outer axles of any two or more consecutive axles. N is the number of axles being considered. All combinations of axles on a vehicle must be within the bridge formula limits.
In addition to the Bridge Formula, federal law limits the weight on any single axle to 20,000 lbs., and axles closer than 96 in. apart are limited to 34,000 lbs.
In some states, gross weight and axle weights may be higher due to "grandfather" rights. This is where things can get complicated. When the federal Bridge Formula limits were set, states were allowed to keep, or grandfather, weight limits that were higher for trucks operating on state roadways.
And some regions of North America don't follow the federal Bridge Formula if you are not on the federal Interstate system.
Consequently, you end up with a patchwork of regulations that make it difficult to optimize a truck that operates across state lines. "Take the Southeast for example," cites Mike Cantwell, Volvo Trucks North America. "Vocational trucks in Georgia are strictly Bridge Formula 20,000-lb. front and 34,000-lb. rear with no lift axles. Alabama allows lift axles and Florida allows front ratings based on tire footprint, which could get you to 22,000 lbs. on the front."
If you're interested in hauling maximum payload and operate in a region that adheres to the Bridge Formula, the length of the wheelbase becomes a critical issue. "Bridge Formula states almost require maximum payload to maximum length or it is costing the owner revenue on every load," says Cantwell.
You really need to look at the regulations in the areas in which you operate and determine what trade-offs are acceptable. "A contractor that operates in several locales needs to take into account the types of roads he travels on, as well as his application and payload," says T.J. Reed, product manager, Western Star.
No matter what local regulations drive your truck configurations, you must adhere to a few basic guidelines. The Gross Axle Weight Rating (GAWR) determines the maximum load for each individual axle, and the GVWR must not exceed the capacity of the individual axle ratings.
Front axle selection
Axle-forward trucks provide a longer wheelbase when compared to an axle-back chassis with the same overall truck length; this allows maximum payload when operating under the Bridge Formula. The mix of axle-forward vs. axle-back trucks sold proves most contractors are bound by the formula.
"I thought we would reach 25% axle-back production due to its desirability in those states where the Bridge Formula is not being enforced," states Steve Ginter, vocational product manager, Mack Trucks, Inc. But apparently more contractors are using roads that require the Bridge Formula to be followed. "In 2006, we built five axle forwards for every axle back." He now states that the market will probably settle at 20% axle back and 80% axle forward.
There are other variables that can dictate whether you should choose an axle-forward or axle-back front axle configuration. "Many customers like the looks of the axle forward over the axle back," says Cantwell. "It is also better for the secondary or resale market to allow resale into different markets. The axle forward also allows the fuel tanks and battery box to be further forward."
However, if local regulations allow, an axle-back configuration offers several key benefits. "If you are free to use the axle back, the advantages over the axle forward are reduced turning radius because of the axle position, and you are also going to have greater payload transfer to the front axle," says Ginter.
The goal is to optimize weight distribution. "The axle-back vehicle will load the front axle sooner since it is closer to the load. Therefore, to get the maximum GVWR, you may need to lengthen the wheelbase," says Cantwell. "Once you load the front axle to its maximum, unless you make a special body (higher sides), you will probably need to lengthen the truck to fully load the rear."
Taking the best advantage of the GAWR on the front axle allows you to get closer to the overall GVWR in areas where you don't have to follow Bridge Law requirements. "It's easier to get maximum GVWR with an axle-back configuration," says Reed. "For example, if a contractor is getting paid to haul cargo by the ton, he'd prefer to spec a set-back axle so he can haul more."
The additional payload with an axle back also makes front axle capacity an important consideration, with many choosing to opt for a 20,000-lb. front axle. "With an axle back, you know it is easier to load the steer axle to maximum capacity," says Reed. "That means you would not want to penalize yourself by under spec'ing with an 18,000-lb. front axle. By spec'ing a 20,000-lb. axle in lieu of an 18,000-lb. axle, you have very limited cost and weight penalty between the two."
Maneuverability of an axle-back truck is also better given a comparable configuration. "In most cases, the vehicle would have better turn angles being an axle back [depending upon wheels and tires]," says Cantwell. "Many trucks will lose about 5° turn angle with axle forward. This is using the 29-in. front axle set back. [Some manufacturers don't use 29 in.] We do have wheel equipment that will maintain the same wheel cut on axle forward/axle back if that size tire is required."
In many cases, maneuverability is more complicated than simply measuring wheel cut on an axle. "At Mack Trucks, we use our engineering specifications where we meet component clearance requirements," says Ginter. "Essentially we have more wheel cut available on the uninstalled axle than there is available on the truck in some cases."
The customer starts by selecting the preferred tire diameter, size and wheel equipment. "During Granite assembly, the Mack technicians set the front axle wheel stops using our engineering general specifications for clearance between steering components (1/2 in.), and other parts of the truck (1 in.)," says Ginter. "By setting the wheel stops in this manner, we are providing the tightest turning radius available for the customer's truck.
"When we have met that specification, we lock it up and now it is set," he continues. "Turning radius will vary because customers select different tires and wheel equipment." Wheelbase length will strongly affect the turning radius.
Pusher and tag axle pros and cons
Pusher and tag axles help increase legal carrying capacity. "You are looking to pay back the cost of the chassis by hauling more tonnage - street legal at maximum payload," says Ginter. "The payload-optimized truck may be able to haul as much as one and a half trucks configured without tags and pushers."
But while they can optimize a truck's legal payload, there is a downside. Adding extra axles can reduce maneuverability on the jobsite. Tire scrub also becomes an issue, adding significant wear.
Auxiliary axles do translate into longer wheelbases. "In order to properly use steerable pushers, the vehicle is naturally longer," says Cantwell.
"Tire scrub and tire wear are always a problem with any pusher axle," he adds. "The weight and cost of the pusher sometimes don't give enough added payload to make it pay for many years, depending upon the state it is used in."
More selections
The selection of lift axles has expanded, Ginter reports. In addition to traditional lift axle capacities, there are more axle ratings being offered that allow you to really optimize the truck for your operation.
Reed notes, "Some of the trends we have seen include 8,000-lb.-capacity lift axles that maximize Bridge Formula while reducing cost and weight as compared to a 13,200-lb.-capacity lift axle."
The ultimate use of pusher and tag axles are the Super 16 and Super 18 dump trucks, which have 16 and 18 wheels, respectively. "These trucks are not as complex as you may think," says Cantwell. "There is a specific wheelbase that makes these work, as well as certain axle spacings that are determined by the body companies based on the capacity allowed."
The use of lightweight components can further increase payload. "A contractor spec'ing a Super 16/18 dump truck can maximize the payload by spec'ing lightweight components, such as frame rails, crossmembers, lift axles, aluminum wheels and more," says Reed. "Talking to a body builder can also help determine how the body's center of gravity affects axle loading."
There are also different drive axle variations to consider for special applications. "Later this year, we are going to be introducing a tridem axle - a tri-drive rear axle," says Ginter. "Tridem axles provide more traction than a conventional tandem axle, but their use does not change the gross vehicle weight restrictions compared to the conventional tandem in some regions."
With so many choices, it can be intimidating to properly spec a truck. Your dealer is the best place to start since it can assist with the necessary calculations.
"Our order spec'ing tool that the dealers use has all the calculations in it to assist the dealer. But knowing how to do it manually always helps for checking," says Cantwell. "Multi-axle trucks are much harder. You need to figure the weights with the axles up and down, plus space everything to the limitations of the lift axles, as well as limitations different states put on lift axles."