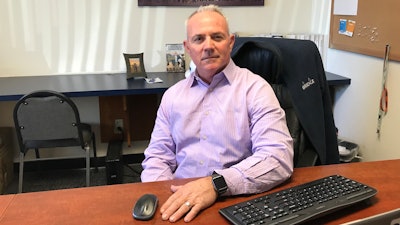
by G.C. Skipper, Contributing Editor
Mason Ford, CEM, director of equipment and 19-year veteran of Skanska USA, will become AEMP’s 2019-2020 Chairman of the Board when AEMP convenes in March. He’s more than ready to take on the job.
Ford recognizes that not all association members, “put things in the ground,” and each point of the Equipment Triangle functions in individual and distinct ways.
Fleet managers themselves have totally different game plans for meeting the demands of their specific operations. But the most pressing challenges in the industry, regardless of what the fleet is used for, Ford says, are:
- Getting the work done, the equipment maintained and on the job site, and
- “Dealing with all the distractions that wrap themselves around doing the job.”
By distractions, he means implementing technology, recognizing and making adjustments to recruit and retain a work force that has changed dramatically. Today’s talent pool is filled with a generation already adept in the use of technology that remains unfamiliar to some industry veterans.
The work and each distraction must be dealt with differently and separately.
Ford says overcoming distractions is a very long, slow process, but at some point it becomes part of the work itself.
“It’s almost like we’re running two very different companies at the same time,” he comments.
The basic solution to the situation is to determine what is important and how best to handle the distractions; to maintain some balance between working “in” the business and working “on” the business.
“The answer to how that’s done is to turn the distraction part of the job over to the staff and let them focus on that,” Ford says. “As they develop, the distractions themselves become useable or value-added processes.
“What AEMP has been tackling so far is a perfect example of what I’m saying. The noise right now for AEMP is technology, and member demands for us to act as a go-between for all interested parties.”
The association is staffing right now to go down this road. Everything in the world is changing: the technology, the business model, the new labor generation and the way we do business.
“With these changes, it is so important for us to focus on putting work in the ground, rather than taking the easy way out by adding layer upon layer of stuff when, you might say, there isn’t a cake. Once you have the cake, then you can add the icing, sprinkles and whip cream.”
Managerial styles vary broadly. Some managers focus on finance and get wrapped up in cash flow. Others get wrapped up in technology and the application of technology.
“But at the end of the day,” Ford says, “it’s about each of us providing reliable, safe equipment to execute the work. Period.
“Technology or no technology, the basics remain. Someone still needs to inspect the machine before an operator climbs into the cab and puts the machine in motion.”
How fleet managers can avoid being sidetracked by distractions in the first place is still a gigantic question mark simply because there are as many different applications as there are managers.
“I don’t know how to answer that question, other than to say this: when I look at the people in our organization who work with or for me, I know there is a core of disciplined (I’ll call them old school) equipment managers who really keep their eye on the ball. They make sure the work gets done. Certainly, you need the basic ingredients, which comes down to this. I don’t care what technology you are using, the foundation of equipment operations and management rests on training operators and doing daily and routine inspections of equipment. Those two items are the basis of everything we do. And when you feed that back into design and engineering and manufacturing of equipment, you wind up with a good product that’s actually doing the work.”
Ford says there is still nothing in the world that can substitute for hands-on experience.
“Perhaps the message we should get out there for a discussion is how important these experienced people are when it comes to successfully making the transitions necessary to cope with all these changes.”
Experienced workers sometimes must take their eye off the ball to help deal with today’s technology. That is necessary to being able to adjust and adapt to the increasing frequency of changes constantly peppering the industry.
Ford has no doubt about what he wants to accomplish in his new role at AEMP. “I want us to keep doing exactly what we’re doing now,” he says. “We need to complete the alignment of our mission, our vision, our strategy and our product. All of them should be completely aligned.”
Another major change is the retirement of Stan and Cindy Orr. “They have done a great job and have always been there as a resource to provide AEMP with important, sometimes critical, but always necessary, information.
“Their guidance, recommendations and support of our strategy, the help they’ve provided in driving our finances and the intangibles, and using a little intuition and feel when it’s called for – that goes along with the job. They have successfully processed the data and input into result-oriented initiatives, which have greatly benefitted the association’s ability to change with the times, making sure we have what we need when those changes come. AEMP already has started that.”
As one of Ford’s colleague’s remarks, “He has the knowledge and the passion to handle the responsibilities that come with the position.”
“Now it’s time to hand off the ball to a new quarterback,” Ford says.