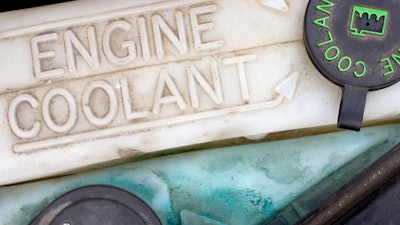
New advanced engines and cooling systems are changing cooling system maintenance requirements. Service technicians and fleet managers should review their preventative maintenance (PM) strategy and incorporate changes needed to maintain these advanced systems.
A cooling system is designed to circulate a cooling medium which absorbs heat from the engine and dissipates it through a heat exchanger (radiator or cooler). If a problem in the cooling system hinders this removal of heat from the engine, equipment issues and eventually engine failure will occur. In fact, it’s estimated that 40% of all engine problems originate in the cooling system.
Unfortunately, damage to the cooling system is often difficult to see until it’s too late. Some problems include:
- Corrosion
- Liner cavitation
- Premature failure of the head gasket, water pump, radiator and other critical components
- Engine failure
Read next: Cooling System Maintenance Keeps Diesel Engines Out of the Heat
What is the purpose of coolant?
One of the primary functions of coolant is to regulate heat within the cylinder head and engine block. Coolant picks up heat and transfers it to the radiator. Coolant is also used to protect against freezing and boiling, and corrosion and pitting of cylinder liners and the engine block.
One of the most important parts of maintaining a cooling system is the coolant or antifreeze itself. Ensuring you have the right balance of water and glycol is essential.
Do not use water instead of coolant, it can cause the cooling system to corrode. If coolant isn’t available and water must be used, it should be used with a corrosion resistor. And never add tap water to a cooling system.
Tap water contains minerals and other contaminants that are not good for the cooling system. Only used deionized water. If you must use tap water in an emergency, make sure to flush the system and replace the coolant as soon as practical.
According to Chevron, there are different types of coolant, including conventional low-silicate, fully-formulated and extended life coolants (ELC).
Read next: Do You Know Your ABCs of Heavy-duty Coolants?
Conventional low-silicate coolants, often called “green antifreeze,” is a glycol-based product known as inorganic additive technology (IAT) and contains silicates as part of its inhibitor package. This is your typical "green antifreeze." This type of coolant inhibits corrosion by laying down a chemical layer over the metallic surfaces of the cooling system. However, this layer can impede heat exchange and shorten the life of the water pump due to scale buildup, according to Chevron.
Fully-formulated coolants feature the addition of a pre-charge of supplemental coolant additives (SCAs) designed to protect cylinder liners in heavy-duty engines from cavitation. To maintain this protection, these types of coolants require the addition of SCAs periodically throughout the coolant’s life. But be aware, the total dissolved solids in circulation can result in pump vane and seal wear. These coolants can be green, pink or purple in color.
ELCs are designed with special chemistries to prevent liner cavitation from occurring throughout the coolant life without the need for SCAs. These types of coolants can be nitrited (NOAT), which are typically red in color, or nitrite-free (OAT), which vary in colors. Unlike the coolants mentioned above, ELCs do not contain solid additives and will not decrease pump life.
A third type of ELC is hybrid organic additive technology (HOAT), which features an inhibitor package combining IAT and OAT chemistries.
Fleet managers and technicians need to understand which type of coolant is used in your equipment in order to maintain it appropriately. Coolant types should not be mixed as some types are not compatible and can even create a gel that results in system failure.
Read next: Antifreeze Balance is Key in Coolant System Maintenance
Cooling system maintenance is changing
In the past, cooling system maintenance was relatively simple. Most maintenance technicians could just look to see if the coolant level was visible, and if so no further action was recommended.
As long as no visible evidence of leakage was seen at the hose connections and water pump and no steam was present while the engine was running, maintenance was likely not done. The most typical maintenance needed was replacing the radiator cap and topping off the coolant level.
However, the advanced engines of today require more of the cooling system, and that means cooling system maintenance is changing as well.
According to an article from Work Truck, cooling system maintenance starts when you take possession of a piece of equipment. Maintenance professionals need to know which types of coolant are present from factory filled engines in order to prevent cross-mixing coolant types. Consider labeling the radiator to indicate which coolant type is permitted in the engine.
If you are unable to use the same coolant, Polaris Labs recommends selecting a coolant with similar corrosion protection inhibitors to maintain the inhibitor levels for adequate corrosion protection.
Additionally, if your coolant includes SCAs, coolant testing to ensure high enough SCA levels will be needed.
Despite their longevity, extended life coolants are not maintenance free. These coolants should be tested twice a year to confirm color, concentration, pH and carboxylate levels.
Best practices for cooling system maintenance
Routine maintenance recommendations may vary from one engine OEM to another, but there are some general maintenance guidelines to follow with cooling systems. One best practice tip is to check coolant and cooling systems during routine oil changes.
Here are a few additional cooling system maintenance check points:
- Ensure cooling system is filled with coolant and freeze protection level is adequate for the ambient environment. Under-filling the cooling system can cause corrosion and overheating issues. An inadequate freeze protection level can result in cracking of lines or passages when the coolant freezes and expands. If the coolant level is low, investigate why. Many failures happen because of head gasket leaks where the coolant seeps into the engine cylinder and eventually ends up contaminating the engine oil. For Tier IVi and Tier IVF engines, you also need to check for exhaust gas recirculation (EGR) and nitrogen reduction system (NRS) cooler leaks. There are no indicators such as white exhaust smoke or signs in your engine oil analysis that indicate these leaks. They show up as a slow but constant coolant loss. But if the leaks continue they can damage intake, intake valves and the diesel particulate filter (DPF).
- Use the same coolant found in the engine for top offs. Don’t mix coolant types.
- Check radiator fluid levels and concentration. Check the integrity of the radiator cap and look for leaks.
- Have coolant samples analyzed at recommended intervals (check with engine OEM or coolant supplier)
- Properly clean and flush the system when coolant is changed. While flushing the system is a good practice, some coolant problems can’t be fixed by flushing, including corrosion, deposits, pitting and erosion. Flushing should not be the only maintenance practice service technicians rely on.
For the coolant itself, maintenance technicians should do periodic testing of coolant chemistry and adhere to strict and proper drain and refill intervals. Your coolant supplier should be a great resource to verify your preventive maintenance processes.
Polaris Labs also recommends proper testing of coolant formulation be done to see the whole picture of corrosion protection levels, equipment health and contamination that may be present in the cooling system.
Testing is an essential step in cooling system maintenance. Consulting with your coolant provider or engine OEM can help you determine the right testing process for your cooling system.
Read next: Tips to Set Up Oil Analysis Program for Successful Predictive Maintenance
Coolant analysis
Coolant analysis can help you better manage your cooling system and the health of your equipment by catching problems before they cause damage. Maintaining proper coolant levels and properties is essential to preventing engine failure. Coolant analysis is recommended as part of the normal PM strategy. Just changing your coolant regularly will not help identify cooling system problems.
According to Polaris Labs, engine coolant should be tested once before winter and once before summer.
With coolant analysis, you can detect issues including:
- Incorrect glycol concentration
- Unacceptable pH levels
- Inadequate corrosion protection inhibitors
- Sources of contamination
- Early failure
Plus, a coolant analysis program can also help catch problems that are not the fault of the coolant but can cause cooling system failures.
Coolant analysis starts with taking the best coolant sample possible. Polaris Labs offers a few tips when taking coolant samples:
- Sample bottle needs to be clean and free of contaminants
- Fill out all equipment and fluid information completely and accurately whether recording electronically or on paper
- Include the time/distance on both the equipment and the coolant
Replacing coolant filters
Engine cooling systems may include a coolant filter (called a water filter in the past). Changing these filters at every PM interval is not recommended. Instead, coolant filter replacement should be contingent on the level of SCAs present, according to Work Truck.
Premature filter replacement could result in premature release of unneeded SCAs, which could damage the cooling system.
Preventative maintenance is key to the health of your construction equipment, and cooling system maintenance should be part of your PM strategy. As engines and cooling systems continue to advance, revisit your PM strategy to ensure you’ve got the right processes in place to keep your cooling system working productively.