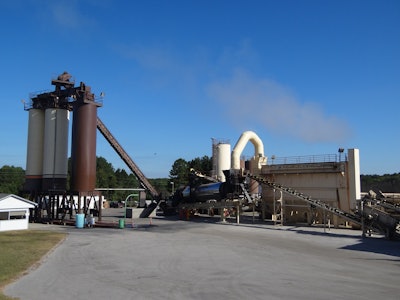
On June 23, OSHA's Silica Rule general industry standard goes into effect for asphalt mix production facilities. At that time, all facilities should have identified and/or documented respirable crystalline silica exposure levels for workers engaged in dust-generating activities or dusty environments.
OSHA spent decades finalizing the rule and setting the permissible exposure limit (PEL) to 50 micrograms per cubic meter. This is a five-fold reduction from what it used to be in the construction sector and a two-fold decrease from what it was for the general industry so it's been a challenge to make sure exposures across construction industry are controlled at that new PEL.
Employee exposure must be below the PEL for all activities using the Table 1 engineering controls for the construction sector. Read this article for more on complying with the silica dust rule on the asphalt construction side.
Compliance at the your production facility, including the asphalt plant and quality control labs, fall under the general industry standard and compliance there is different.
"Millings from the roads that are coming back to the plant and being utilized is now something we're going to have to handle as a part of the general industry silica rule," Chuck Moll, HSE director at Kokosing Materials Inc. says. "Identifying hazards is an important way to understand your exposure and how to handle it."
Assessing Exposure
Anyone who falls under the 1910.1053 rule for the general industry will need to comply with all occupational exposure to respirable crystalline silica.
The employer shall assess the exposure of each employee who is or may reasonably be expected to be exposed to respirable silica at or above the action level.
"On the general industry side, we don't have a Table 1 to go by," Moll says. "Therefore, we need to evaluate every task we have out there and indicate what level silica exposure you might have."
In order to determine how to comply, you first need to figure out where exposure might be. You can start by conducting a visual assessment of your facility. Where is dust present? Does it have the potential to contain silica? You can use a real-time dust monitor. It won't give you the silica content, but it will indicate that you should do some additional sampling to determine any potential exposure.
Areas that May Contribute to Silica Exposure:
1. Virgin Aggregates: The dust could be a potential silica hazard
- How is your aggregate delivered or moved?
- Do you have an open cab loader?
- What weather conditions do you have outside?
2. RAP Piles: Materials on the roadways that are trucked back and moved could be a potential silica hazard
- Do you crush recycled asphalt pavement (RAP) on site?
- Do you utilize open cab equipment to move RAP?
3. Plant Roadways: Sweeping and brooming along the plant roadway could be a potential silica hazard
- Placing water on the roadway before performing these actions can reduce exposure
4. Daily Operations:
- Do you have employees on the ground?
- Where do you have potential aggregate dust?
- What are the responsibilities of the ground personnel?
- Test different tasks and see where their might be exposure based on daily tasks
5. Baghouse & Dust System:
- What is your task?
- What is your potential respirable silica exposure?
- Maintenance personnel are at a risk based on the tasks they are doing
6. Drum Systems:
- What type of drum system do you have?
- When and where is your potential exposure?
7. RAP Systems:
- What type of RAP system do you have?
- Do you have an inline crusher?
8. Drags & Silos:
- Are you in production or maintenance?
"Most of silica exposure is going to be during your maintenance time frame," Moll says. "Working within the drums, baghouses, etc. That's when you're going to get that potential exposure and that's where we tested our air quality."
9. Quality Control Labs:
- What test are being performed?
- Do you have a silica exposure?
"All of these potential tasks being done at the asphalt plant need to be looked at for potential silica exposure," Moll says. "Each potential exposure needs a written exposure control plan."
The two most common ways to determine exposure are through objective data – that is, exposure data available or published for similar activities – or through direct exposure assessment of worker activities. The latter can include surrogate exposures of, for example, respirable dust.
For objective data, as employer shall make and maintain records to include :
- The crystalline silica-containing material in question (data can be obtained from MSDS sheets)
- The source of the objective data
- The testing protocol and results of testing
- A description of the process, task, activity, material, or exposures on which the objective data were based
- Other data relevant to the process, task, activity, material or exposure
"It was very difficult for us to get this data," Moll says. "When you're running material through the asphalt plant, it's very difficult to know how much of that silica is getting fractionated out so we ended up opting for the assessment exposure testing instead."
Through an exposure assessment, asphalt plants can determine what their exposure is and take steps to comply from there.
If during initial air monitoring, the plant finds levels below the action level of < 25 ug/m3 as an 8-hour TWA then no additional monitoring is required.
If you find that levels are between 25 ug/m3 and 50 ug/m3 as an 8-hour TWA , then:
- a retest is required within 6 months of the most recent test
- Minimum three test required
If monitoring is above > 50 ug/m3 as an 8-hour TWA :
- Retest required within 3 months of the most recent test to make sure controls are effective
- Minimum three test required
During air quality monitoring, the employer shall make and maintain records to include
- The date of measurement for each sample taken
- The task monitored
- Sampling and analytical methods used
- Number, duration, and results of samples taken
- Identity of the laboratory that performed the analysis
- Type of PPE worn
- Name, SSN and job classification of all employees represented by the monitoring and actually monitored
Methods of Compliance
Again, since the general industry does not have a Table 1 to abide by, asphalt plants need to determine what they need to test for, where they need to collect data from and how they are going to comply. The general industry has 15 working days to notify employees of exposure results.
From those air quality tests, plants can look at the work practices they need to change and engineering controls they should install to reduce exposure to below the PEL. If the PEL is still not reached respirators shall be used in conjunction with engineering and work practices . Obligations for engineering controls commences June 23, 2021.
"This gives us some time in regards to putting in different types of engineering controls, dust collection systems and other methods for conducting maintenance," Moll adds.
Under the general industry rule, there also needs to be a regulated area, demarcated by the employer, where an employees exposure to airborne concentrations of respirable crystalline silica exceeds, or can reasonably be expected to exceed the PEL.Under the general industry rule, there also needs to be a regulated area, demarcated by the employer, where an employees exposure to airborne concentrations of respirable crystalline silica exceeds, or can reasonably be expected to exceed the PEL.
"That's something that is different on the general industry side," Moll says. "You need to make sure you have signs up that indicates where regulated areas are, areas where there is potential hazards to silica exposure."
Personal protective equipment (PPE) and controls must also be in place for when workers do have to enter these areas.
The general industry rule indicates companies must also have a written exposure control plan. The plan should contain:
- Description of the task that involve exposure to respirable silica
- Description of the engineering controls, work practices, and respiratory protection required to limit exposure per task
- Description of housekeeping measures used to limit exposure
Since the exposure plan is written by task, you do not need a "competent person" on site to ensure the plan is being executed as long as you have the written exposure plan on site for your facility.
Other Rules for General Industry
The General Industry rule also says that asphalt plants must comply in these areas:
1. Housekeeping:
Employer shall not allow dry sweeping or dry brushing where such activity could contribute to silica exposure
- Alternatives –wet sweeping, HEPA filter vacuuming
Employer shall not allow compressed air to be used to clean clothing or surfaces where such activity could contribute to employee exposure
- Unless used in conjunction with ventilation system
2. Medical Surveillance:
Employer must provide medical surveillance for all employees exposed above the action level for 30 or more days a year . The medical surveillance must be:
- Two dates for the medical surveillance program
- Exposure above the PEL for 30 or more days a year from June 23, 2018 through June 22, 2020
- Exposure at or above the action level for 30 or more days a year beginning June 23, 2020
- Include a medical and work history
- A physical exam; focused on the respiratory system
- Digital or film chest x-ray
- A lung function (spirometry) test
- Testing for latent tuberculosis infection
- Any other test deemed necessary by the PLHCP
- Provided at no cost to the employee
- At a reasonable time and place
- Shall ensure the exam is performed by a PLHCP (physician or other licensed health care professional)
- Medical examinations shall be available at least every three years, or more frequently if recommended by the PLHCP
3. Training:
Employees shall demonstrate knowledge and understanding of
- Health hazards associated with respirable crystalline silica
- Specific task that could result in exposure
- Knowledge and understanding of the written exposure control plans
- Purpose and description of the medical surveillance program
Once you've figured out where there is potential exposure, asphalt plants need to come up with a plan of action.
What tests did you conduct that proved exposure was above the PEL? What type of action level do you need to put in place or what controls are needed to be compliant? Decide what the engineering or work practice controls need to be put in place based on that.
"We have a couple of years before the engineering controls need to be in place," Moll says. "Maybe you decide to change your procedures all together on how you perform winter maintenance in order to be compliant."
For more information, visit http://www.asphaltpavement.org/silica